The primary objective for developing ARGO-HYTOS’ EXAPOR MAX 2 filter element was greater machine availability, longer service intervals, lower-cost spare parts, and lower operating costs for machine operators in the area of mobile and industrial hydraulics.
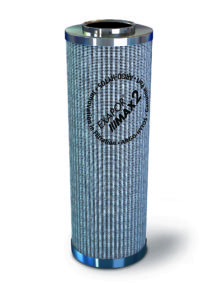
EXAPOR MAX 2 filter elements create higher dirt holding capacity to extend the filter element changeover. This increases the operating reliability and service life reserve for wind power plants with time-based maintenance intervals.
To improve the performance density of the filters, ARGO-HYTOS engineers took a closer look at the conditions in the fold channel. Here, they found the factors responsible for pressure loss in the folded material. The result was a web technology for creating a hybrid fabric that ensures a consistent and optimal opening of the fold channels. Pressure loss in the fold is reduced by as much as 50%. These results were confirmed in numerous trials.
When configuring hydraulic systems, a smaller filter size can be used depending on the application. Pressure loss reduction means bypass valves open less often and for a shorter periods. Consequently, fewer particles get through the bypass to the pure oil side.
The structure of the 3-layer filter material consists of various fine glass and polyester fibers. This new type of material matrix in the pre-filter and ultra-fine filter materials of the EXAPOR MAX 2 filter elements may improve clogging capacity by as much as 60% in filter fineness 5 µm(c).
The unusually low differential pressure and the high clogging capacity of the EXAPOR MAX 2 filter elements enable long service intervals and better cold start characteristics.
In hydraulic pitch adjustment systems, for example, filter elements are subject to strong flexural fatigue stress induced by volume flow and pressure fluctuations. Due to the flow rate fluctuations, differential pressure changes occur on the filter element, which results in the flexural fatigue stresses. The fabric that has been developed and patented for the EXAPOR MAX 2 filter consists of a mix of stainless steel and polyester fibers. The stainless steel threads arranged longitudinally ensure dissipation of electrostatic charges, preventing damage to the filter material and the compromising of oil purity. The polyester fibers arranged transverse to the metal threads ensure optimal flexural fatigue strength and avoidance of fatigue failure.
The plastic sheathing shrink-fit on the filter bellows improves technical aspects and enhances the visual impression of the filter elements. The plastic sheathing is customer-specific and individually imprinted. All EXAPOR®MAX 2 filter elements are fitted with this feature which clearly increases the recognition value of the filter elements. This is just one of the many copy protection measures designed to protect the products and the customers.
Benefits:
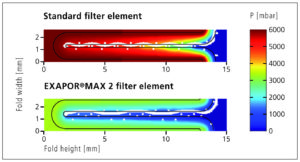
Simulation graphic of the pressure relationships in the fold of a filter element (sectional view).
The perimeter of the fold is shown in black and the support fabric is shown in white.
Increased operational reliability: The risk of sudden machine failure and downtime of wind energy plants can be significantly reduced. Maintenance intervals can be extended, resulting in significant cost and time savings.
Filter element changeover period can be extended because of the higher dirt holding capacity. This increases the operating reliability and service life reserve for wind power plants with time-based maintenance intervals.
Improved oil cleanliness extends the wear service life of components and of the hydraulic and lubricating oils.
Significant reduction in pressure loss combined with improved dirt holding capacity results in a higher performance density that enables the use of smaller filters, depending on the application.
In the fight against product pirates the increased copy protection thanks to customized geometries of EXAPOR MAX 2 filter elements is an important feature for expanding and assuring the strategic spare part business.
ARGO-HYTOS
www.argo-hytos.com
The post Better performance density for filters from ARGO-HYTOS appeared first on Sealing & Contamination Control Tips.
Filed Under: Filtration/Contamination Control, Sealing & Contamination Control Tips