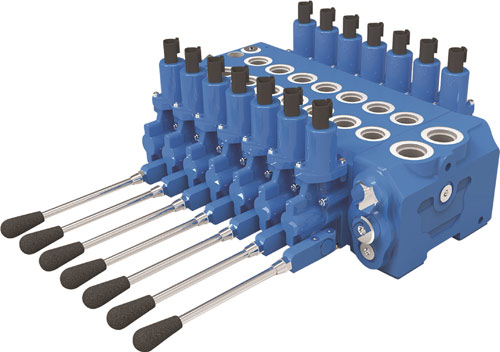
Eaton’s compact and modular CLS valve banks have up to 10 sections to minimize machine space.
It’s no secret that OEMs are looking to build more “intelligence” into mobile and industrial machines. The goal is to make the equipment they sell more productive and efficient, safer, and easier to operate and maintain. With that in mind, power-management company Eaton recently introduced its Dynamic Machine Control approach to designing smarter machines.
According to Andreas Kling, product marketing manager with the company’s Hydraulic Group, Dynamic Machine Control (DMC) is Eaton’s strategy of marrying electronic controls and software with hydraulics and mechanical systems. DMC is not only about precision control of a machine, it’s a combination of higher productivity and efficiency, enhanced safety, more flexibility and less downtime, he explained. In mobile equipment, for example, it equates to lower fuel consumption, lower emissions, faster cycle times, safer operation, easy-to-access data metrics and condition monitoring. “It’s a way to optimize performance and quality and controllability of the machine, and that is really what the customers are asking of us today,” he said.
DMC is embodied in Eaton’s Pro-FX technology platform, which is a suite of electronic and hydraulic products, software tools and function blocks that lets engineers easily integrate hydraulic components to a machine’s control system. Pro-FX compatible products include pumps, valves, motors, sensors, controllers and HMI displays. These Pro-FX ready products include embedded intelligence, allowing them to interact, adapt and optimize their performance in continually changing conditions.
These products can be linked together by Pro-FX control, an open-platform application development tool, explained Eaton’s Paul Brenner, speaking on a recent Fluid Power World webcast. What differentiates Pro-FX products, said Brenner, is that they’re designed to work out of the box, and they can be easily matched together and work seamlessly. That greatly streamlines the process of developing software for a customer’s unique application. “Essentially, our hydraulic products and electronic control developments are closely connected throughout the various stages of the design process,” said Brenner.
One example, Eaton’s new CLS load-sense sectional mobile valve, allows work functions to be prioritized to improve performance and efficiency. The electronics-capable valve integrates with Eaton’s Pro-FX technology platform for applications that require advanced control capabilities, such as excavators, forestry and ag equipment, and truck-mounted cranes. Features include priority flow sharing and local load-sense relief on each section, letting OEMs design valve banks tailored to meet specific machine requirements. And, according to Eaton officials, CLS is highly modular and offers one of the smallest envelopes in the industry.
Pre- and post-compensated flow-sharing sections are available in the same valve assembly, an advantage because the operator sends the right amount of power exactly where it is needed, explained Kling. It ensures priority functions like steering or speed are maintained while others are reduced proportionally. A patented load-sense bleed-off eliminates continuous bleed-off, reducing energy loss and increasing responsiveness. Four frame sizes handle flows from 100 to 350 lpm with maximum pressures from 350 to 550 bar.
Another example of Pro-FX products is the
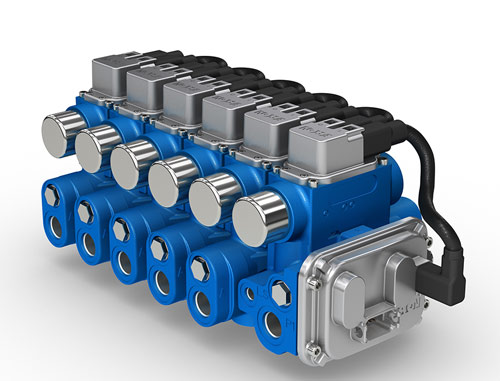
Eaton’s CMA Advanced Mobile Valve, which provides design flexibility and access to real-time operating data for more precise control.
Integrating electronics and sophisticated software into the CMA reportedly helps OEMs streamline the design process, reduce setup time and optimize operation.
The Pro-FX platform lets engineers access software libraries and enable common application functions right on the valve, reducing development time. Designers can also quickly test and electronically tune performance parameters, rather than facing a tedious manual process. CMA readily integrates with other Pro-FX products such as displays and controllers, resulting in system-wide performance benefits.
The valve itself includes an electronics module—essentially the valve’s main controller—explained Nadine Powell, Eaton Hydraulics global product manager for the CMA. It monitors each valve section and stores back-up parameters in the event of a failure or changeout. Electronics capabilities result in fast dynamic response, at only 24 msec.
A twin-spool construction lets users independently control meter-in and meter-out flow to an actuator. While traditional mobile valves require a system to compromise between meter-in and meter-out flow in changing load conditions, the CMA valve senses load conditions and implements proprietary control strategies that optimize performance and reduce parasitic losses on the machine.
Other features include built-in work-port pressure, spool-position, and temperature sensors, and control via J-1939 or CAN Open communication protocols. Integrated sensors let users easily change operating parameters through software, explained Powell, such as limiting maximum pressure based on the application. “And with all those sensors, we really have positioned ourselves with this valve to have advanced diagnostics and servicing capabilities,” she said.
“So parameters such as inlet conditions, spool position and oil flow can all be monitored and reported to customers through this valve,” Powell explained. “Finally, we have the capabilities to do some predictive control behavior. If you have the capabilities to monitor pressure and flow of the valve, you’re getting some monitoring capabilities of other hydraulic components within the system. Everything is programmed through this valve through software, and we have set up a number of advanced algorithms. Some are basic software that we offer within the package, others are optional pieces of software. This valve really offers an OEM versatility, and multi-mode functionality,” she said.
The CMA is available in two frame sizes, rated at 90 and 200 lpm flow and pressures to 440 bar. Common applications include concrete-pump trucks, refuse and utility trucks, telehandlers, all-terrain cranes, drill rigs, excavators and paving machines.
Eaton Hydraulics
www.eaton.com/hydraulics
Filed Under: Mobile Hydraulic Tips