True story: a fiberglass parts plant was having air pressure problems in their plant, so much so that they had turned their air compressor up to 140 psi. This was the highest it could go, which made it consume 15% more power. But still, their most critical air tool was having performance problems.
An air auditor investigated and found that the air tool in question needed about 25 cfm at 90 psi to run at peak performance. The auditor rigged up a test pressure gauge by placing it on a T connection right at the air inlet of the tool. When he pulled the trigger the air pressure fell to 44 psi.
Looking back from the tool to the main compressed air distribution line, the auditor found 50 feet of ¼-in. hose and three quick connect couplers, all undersized for the tool flow. This tool was poorly connected to the system resulting in greatly decreased performance.
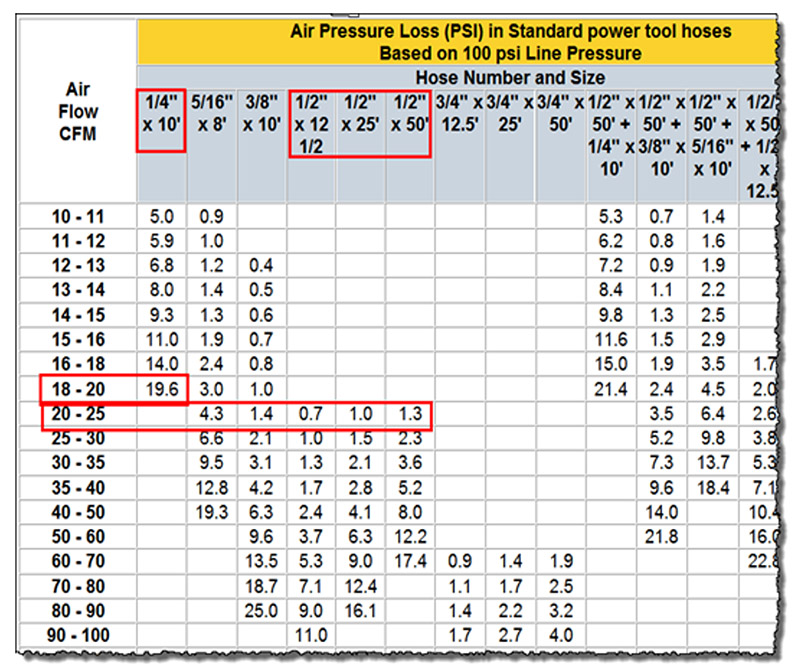
The supply hosing was upgraded to 3/8-in. and the resulting tool pressure when running settled above 90 psi, even when the compressor discharge pressure was reduced to 110 psi to save energy. This greatly increased tool performance.
The table shown in the graphic shows the huge effect going to larger size hose has on the pressure drop. Use this to help improve your system.
Filed Under: Hose & Tubing, Pneumatic Tips