Compressed air systems naturally generate condensate as moisture in the air condenses during compression and cooling. If this condensate is not properly managed, it can accumulate in the system, particularly in uninsulated outdoor pipes. During winter, when temperatures drop below freezing, this condensate can turn into ice, leading to significant operational and safety issues.
Freezing condensate in pipes can create blockages, restricting or completely stopping the flow of compressed air. This not only disrupts operations but can also cause equipment downstream to malfunction due to insufficient air supply. Blocked pipes may also lead to a dangerous buildup of pressure, increasing the risk of pipe bursts or system failures that require costly repairs and downtime.
Moreover, ice formation inside pipes can damage the system’s components, such as valves, fittings, and connections, by causing cracks or leaks. Over time, this can lead to increased maintenance costs and reduced efficiency. To avoid these issues, it is crucial to implement proper condensate management, such as using reliable drains, ensuring adequate insulation, and maintaining air dryers to remove moisture from the air. By addressing condensate effectively, you can protect the integrity and performance of your compressed air system, even in harsh winter conditions.
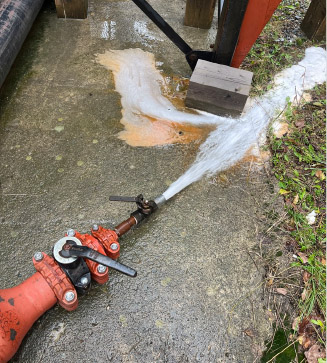
To prevent freezing and ensure reliable operation of outdoor compressed air piping in winter, it’s essential to remove moisture effectively. This begins with upstream air dryers, such as refrigerated dryers for general applications or desiccant dryers for sub-freezing conditions, which lower the air’s moisture content significantly. Additionally, automatic condensate drains should be installed at low points and near separators to remove accumulated water. Heated or insulated drains are especially useful for preventing freeze-related blockages.
Complementary measures include sloping pipes to direct water to drain points and using coalescing filters with moisture traps to capture residual water and oil. Insulating or heat-tracing pipes helps maintain air temperature above freezing, reducing condensation risks. Monitoring dew point levels ensures the system stays within acceptable limits, allowing for adjustments to dryers or filters as needed. These steps collectively protect the system from freezing, maintain air quality, and avoid costly disruptions.
Filed Under: Air Compressors, Air Preparation, Components Oil Coolers, Compressed Air Technologies, Engineering Basics, Pneumatic Tips