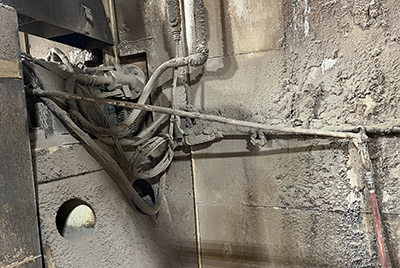
A building products company had constantly overheating bearings on some large fans induced draft in their process and decided to use compressed air to provide some extra cooling. On one fan bearing they installed a spare air wand and tied it in position with wires, so the nozzle pointed directly at the hot bearing, this was done as a temporary measure ten years ago. The trigger of the wand was wired open for continuous flow, the air consumption continuing without interruption, Fig. 1.
For the next fan bearing fix they had become aware of high efficiency compressed air nozzles, so they rigged up a cooler using a specialty nozzle to save energy, Fig. 2. This nozzle had a flexible goose neck used to position the nozzle to provide the best cooling. This again was a temporary measure, but years later the nozzle continued to blow.
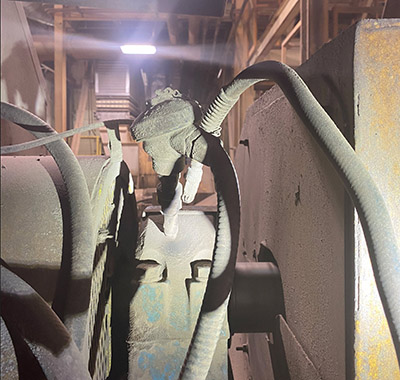
A compressed air assessment was done at the plant and the auditor decided to measure both nozzles. He was surprised to find that the standard air wand consumed 9 cfm while the optimized nozzle consumed 14 cfm, something he had not expected. A look at the installation showed that the standard wand was fitted with a pressure regulator, however, the optimized nozzle used unregulated line pressure. A look into the specifications of the optimized nozzle showed that the rated pressure for the nozzle was 70 psi, but it was running at 110 psi, consuming about 70% more than its catalog rating.
This exercise showed, if we must use compressed air flowing, we should not assume that optimized nozzles will actually save compressed air flow, all nozzles need to be installed correctly and fed with rated pressure.
It turns out that this bearing cooling was determined to be unnecessary, the nozzles were installed years ago but never removed when the bearings were changed. These two items were eliminated, reducing the compressed air load by 23 cfm and saving $4,000 in electricity costs annually.
Filed Under: Components Oil Coolers, Compressed Air Technologies, Pneumatic Tips