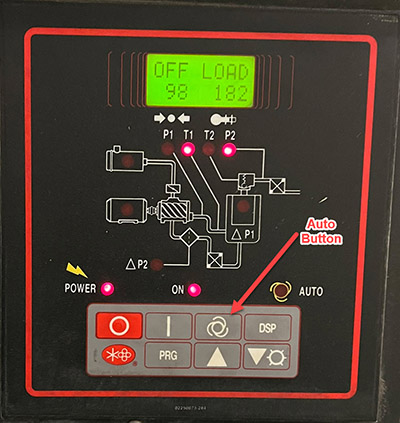
A farm implement manufacturer had a system of three large 150-hp compressors that were air-cooled lubricant-injected screw compressors. To control these compressors — two of which were needed for peak duty on any given day — the compressors were set up in a cascaded pressure band arrangement, with each unit running in load/unload mode. In normal operation, only one compressor takes the trim load, and at the same time the other runs at full load, the most efficient point for an air compressor.
The plant management personnel were given a directive by the company owners to try to find some efficiencies in all their utilities. To address the compressed air system, they brought in a local expert compressed air auditor to have a look.
Instruments were placed on the system to measure pressure, power, and flow — and the captured data told a sad story. The compressed air system was running with poor efficiency, especially during night and weekend shift operation, with levels as high as 40 kW per 100 cfm. When asked if there was anything they could do to improve the number, the auditor held up one finger.
The auditor explained with this one powerful finger he could save the company $15,000 per year. He took the Maintenance Manager over to one of the compressors and pointed to a pushbutton. He explained that by placing the compressor in “Auto Mode” by depressing this one button with his finger, he could save them thousands in electrical and maintenance cost each year.
During night and evening operation, the plant only needs one compressor. Yet both were running, with one staying unloaded, consuming about 40 kW continuously while producing no compressed air. Pushing the button would allow the one compressor to time out and turn off during these hours, allowing it to remain off an estimated 4,000 hours per year.
That’s one valuable finger!
Filed Under: Components Oil Coolers, Compressed Air Technologies, Pneumatic Tips