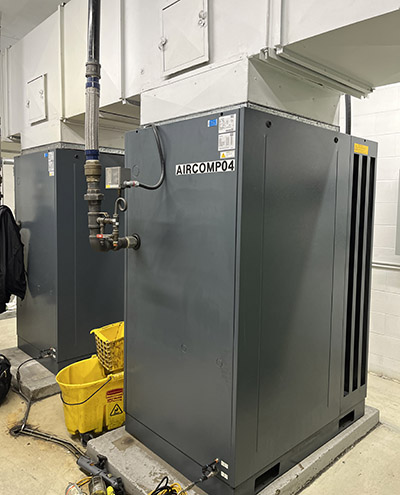
A plastics manufacturer was having constant trouble with his desiccant air dryers. No matter what he did, they would constantly set off dewpoint alarms, which was very annoying. He called in a compressed air auditor to have a look.
The auditor shot temperatures and found that the discharge of the compressors was too hot. Outputs exceeding 120° F contained more water than the air dryers were rated to process, with moisture levels increasing by about double for every 20° F increase. The auditor measured the temperature of the cooling air, this was also excessive, even though the temperature outdoors was only 30° F.
The auditor pointed to the compressor room ventilation inlet duct — it was coming from the plant, where temperatures were near 90° F. He directed the Maintenance Manager’s attention to two electric vacuum pumps in the room that were radiating significant amounts of heat. And he pointed up to the hot air ducting that was connected to the compressor. The large hot surfaces were radiating a significant amount of heat into the room, raising the ventilation air temperature to excessive levels.
The ventilation system designer had not accounted for all sources heat radiation within the room, had chosen a poor source of cooling air, and had no cross ventilation. The compressors were overheating because the cooling air was too hot, overloading the air dryers. Clearly, this was the cause of the constant alarms.
At this site, it was relatively easy to install additional ventilation with thermostatic control to temper the room with cool outside air, but not to subject equipment to freezing winter temperatures. Once this was in place, the Maintenance Manager finally had peace again.
Filed Under: Components Oil Coolers, Compressed Air Technologies, Pneumatic Tips