Feedback in a vacuum-handling system limits product damage and energy consumption.
By Josef Karbassi, Vice President Automation Division, Piab AB, Täby, Sweden
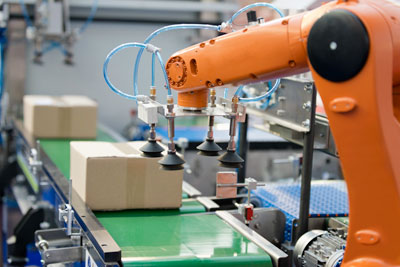
internal feedback tend to be more productive and economical. Image courtesy istockphoto
It goes without saying that optimized systems are the most productive. But optimizing an automated, vacuum-based handling system that must deal with a variety of products and operating conditions is no simple task. That requires “smart” regulation tools. To fully appreciate how such tools can improve a system, let’s take a step back in time.
In the 1830s machinery in Scotland’s textile mills, to function optimally, had to run at a constant and steady temperature. The need for optimization led to the development of the bimetallic thermostat. A thermostat senses the temperature and then automatically regulates the system so that it maintains desired conditions without manual intervention. And records show that simple thermostats were, in fact, already used in the early 17th century to regulate the temperature of incubators for chickens. These first industrial uses of thermostatic regulation are also some of the first examples of feedback-controlled systems.
What, one might ask, do textile mills and poultry incubators have to do with vacuum-based automated handling systems? Well, the latter also benefits from feedback regulation, as this helps to precisely maintain proper operations despite varying conditions. A “smart” vacuum-controlled regulator will sense the vacuum pressure, and then automatically adjust the feed pressure to an air-driven vacuum pump to maintain a set and constant vacuum level. Keeping vacuum pressure constant in automated handling systems ensures a steady grip and helps prevent product damage, speeds production and lowers overall production costs.
Regulating pressure
Suction cups and air-driven vacuum pumps are an unbeatable combination for the automated gripping and handling of items like cardboard boxes. Case or carton erectors and rotary carton machines are widely used throughout industry and, together with robot-driven applications such as palletizing and de-palletizing, these benefit greatly from the winning technology formula of suction cups and air-driven vacuum pumps and ejectors.
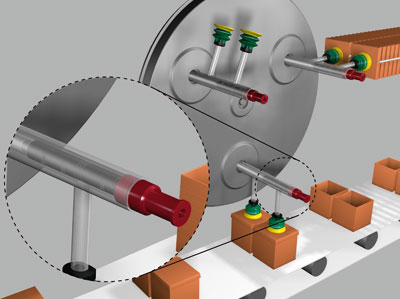
Keeping vacuum pressure constant in rotary feeder systems ensures a steady grip and helps prevent product damage.
However, to keep a safe grip on the boxes without causing damage, it is essential to maintain the vacuum at precisely the right level for each individual box. This is easier said than done, because corrugated cardboard is a porous material; it will leak, but not always at the same rate. The rate of air flow through the material will vary even within a well-defined carton quality.
When using suction cups, air leakage also depends on how well the lip of the suction cup seals onto the corrugated surface. This can vary from one box to another, and from one production cycle to the next.
Traditionally, vacuum-handling systems for corrugated carton materials have been designed for the “worst-case scenario” in terms of leakage. That is, making sure that there is sufficient gripping force every cycle, or for every individual cardboard box. As a result, many systems are substantially oversized and, hence, wasteful in terms of energy consumption for most operating cycles. More money is spent on energy to produce vacuum flow, and larger systems also tend to have higher up-front costs and can hurt productivity.
Limiting force
Another serious drawback is that excessive force can damage the box or product. Suction cups provide a gentle grip compared with many other alternative solutions, and will not damage the cardboard surface if properly used. Lifting force can be controlled by the size of the cup and the vacuum pressure.
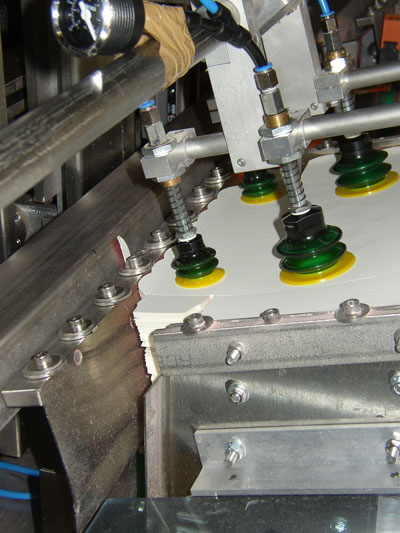
Holding vacuum steady when handling corrugated cardboard minimizes indents or marks and reduces energy consumption.
Damage to the surface of cardboard boxes is related to high vacuum pressure. Thus, there is a balance between the required lifting/handling force and the potential damage to the surface, and it is difficult to fine-tune this balance for each cycle or box.
The surface of a box can be damaged or marked if vacuum pressure increases in the suction cup because leakage flow through the cardboard box is lower than expected, and lower than the average leakage flow of the boxes in a particular cycle. Quite often, needlessly high vacuum pressure is used to achieve sufficient suction force, rather than designing a system with sufficiently large cups.
The solution is to maintain a constant vacuum despite variations in the cardboard material makeup. If a fixed or constant vacuum level can be guaranteed irrespective of cardboard quality in each box, damage or marks can be avoided, while sufficient vacuum pressure will still be present to grip and lift the box and maintain maximum production speed.
Unfortunately, the feed pressure for air-driven vacuum pumps is usually adjusted with a manually controlled air-pressure regulator. The unit regulates high-pressure supply lines and gives a set/regulated constant air pressure to a device—for instance, an air-driven pump—independent of air pressure flow, but not a constant vacuum level.
The above discussion shows that for corrugated-cardboard handling applications with vacuum cups, it would be most gentle (no marks or damage), economical and energy efficient if feed pressure to the air-driven pump could vary from cycle to cycle to keep the vacuum level constant. With a manual-controlled regulator that would require a full-time person adjusting the feed pressure by hand for each cycle—impractical, to say the least.
piSAVE optimize
Piab has addressed this need with the development of a vacuum feedback-controlled air pressure regulator, where a constant vacuum level is set by the operator only once. Tailor-made for air-driven vacuum pumps and ejectors, this smart regulator, called the piSAVE optimize, senses the system vacuum on a sensing port, and then regulates to maintain a constant vacuum level by momentarily increasing or decreasing the air pressure to the vacuum pump.
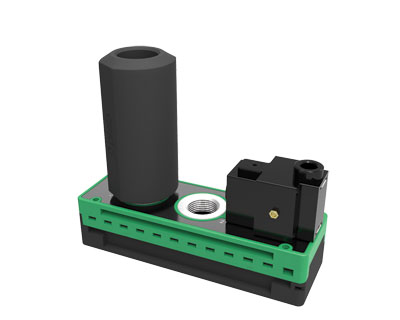
The piSAVE optimize, shown with a piCLASSIC vacuum pump, senses and regulates system pressure to maintain a constant level.
Thus, it automatically adjusts the vacuum pump’s supplied pressure based on the application. Only the necessary amount of compressed air required will be used without sacrificing speed or performance. Initially, the device starts with full pressure until it reaches set vacuum level and ensures full force and pick-up speed when suction cups are applied to the surface.
For a vacuum system handling corrugated cardboard, the piSAVE optimize maintains constant vacuum pressure by adjusting the feed pressure to the air driven vacuum pump, automatically, cycle by cycle. A constant and as-low-as-possible (optimized) vacuum pressure in a system for handling corrugated cardboard will:
- Eliminate risk for damage/marks on the surface.
- Reduce energy consumption in the range of 30 to 50%, which equates to an annual savings of around $125 per installation for a typical handling application.
An oversized vacuum system for handling corrugated cardboard is an effect of varying leakage from carton to carton to handle worst-case conditions. It creates unnecessary deep vacuum pressure (that consumes extra energy) for most cycles/samples, as well as heightens the risk of surface damage.
A constant vacuum level for materials like corrugated cardboard, despite a large leakage variation (both through and over surfaces) cycle by cycle, can now easily be achieved with a new generation of vacuum controlled air-pressure regulator, like the piSAVE optimize.
piSAVE optimize has an operating range for set vacuum levels from 25 to 70 kPa (7.4 to 20.7 in.-Hg). It works with any air-driven pump/ejector that has an air-consumption from approximately 100 to 900 Nl/min (3.5 to 31.8 scfm) at recommended feed pressure. That includes single-stage, air-driven vacuum pumps/ejectors as well as multistage vacuum pumps/ejectors. For circuits with smaller ejectors, one piSAVE optimize can to be used for two or more small ejectors.
Besides the positive energy saving from an environmental perspective, the low difference in price versus a traditional air regulator will pay off in a few months for new installations.
Updating an existing system which already has a regulator will typically pay off in less than a year in a suction-cup handling application for corrugated cardboard.
Materials-handling engineers can now use vacuum feedback-controlled regulation to optimize automated systems based on vacuum ejectors, and to boost their productivity in the process, without compromising on lifting capacity.
Greater vacuum versus larger cups
The gripping and lifting force in a vacuum-cup handling application can be controlled by the size of the cup and the vacuum pressure. For engineers, the general rule is that it is best to keep vacuum pressure as low as possible and the cups as large as possible.
Consider that lifting force from a suction cup is defined by two factors: suction cup area and the vacuum pressure, or F = A x P. Because the area is a “square” unit, it is clear that the force will increase or decrease more by changing the suction cup area versus changing the vacuum pressure. So a small decrease in vacuum pressure will not affect the force much. The simple conclusion for system designers is to use as low a vacuum pressure as possible and as large a suction cup as practical.
Energy calculator details cost savings
Limiting the vacuum pressure on leaking materials like corrugated cardboard boxes can significantly reduce the energy consumption in vacuum pumps. But are the resulting savings worthwhile? Piab’s piSAVE optimize energy calculator helps detail the specific savings.
The online tool first lets the user choose metric or imperial units. One then selects the installed ejector nozzle type. This includes a range of Mini and Midi Coax ejectors, Classic nozzle rows, and numerous nozzles ranging in size from 0.8 to 2.5 mm in diameter.
Next the tool queries for the number of nozzles/nozzle rows, the “vacuum on” and “vacuum off” time for the application, and the operation hours per year. Finally, the user inputs the ejector feed pressure before and after installation of a piSAVE optimize regulator.
The software then outputs the potential energy savings versus a traditional regulator. Note that users often gain additional savings by preventing product damage that could
otherwise be caused by excessive vacuum and force. The energy calculator is available at www.piab.com.
Piab
www.piab.com
Filed Under: Pneumatic Tips