By Ron Marshall
The short answer is “as cool as possible, but not below freezing.” The practical answer is uncomfortably cool, in the range of 50° to 60° F. Keeping the temperature low reduces the amount of condensed moisture in the discharge air and makes things easier for the air dryer.
Compressors generate significant heat during the compression process, a byproduct that can be harnessed to pre-warm cold incoming air rather than using heaters to heat the cooling air. This approach improves the efficiency and reliability of an air-cooled compressor, particularly in cold climates where extreme temperatures can affect performance.
When air is compressed, its temperature rises significantly. Instead of letting this heat dissipate into the environment, a portion of it can be redirected to warm the incoming air stream. This is achieved by routing the cold intake air through a heat exchanger or ducting system that captures and transfers the heat of compression from the compressor’s hot discharge air to the intake air. As the cold air passes through this system, it absorbs heat, ensuring that the intake air is tempered before entering the compressor.
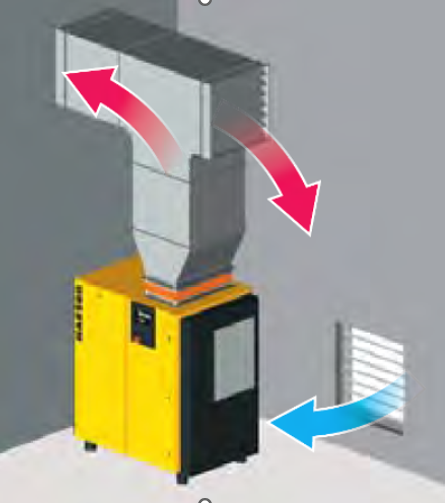
Pre-warming the intake air offers several benefits. It helps prevent condensation in the system, reducing the risk of freezing in cold environments. Warmer intake air also reduces the energy required to compress it, as less work is needed to reach the desired operating temperature. By leveraging the heat of compression, facilities can improve compressor efficiency, lower operating costs, and maintain consistent performance in challenging weather conditions.
If the room has auxiliary heaters, you should ensure that these are not running when there is plenty of compressor heat to use to temper the room. This extra energy can be a big waste of money, especially if the flow of cooling air is significant. Often, in poor installations, the room heaters may consume about as much energy as the air compressors consume.
Use the heat, it’s free — and an excellent byproduct of the compression of air.
Filed Under: Air Compressors, Air Preparation, Components Oil Coolers, Compressed Air Technologies, Engineering Basics, Pneumatic Tips