A hydraulic pump directly coupled with a servomotor delivers highly dynamic performance, often with sizeable energy savings. Machine-tool manufacturer Lasco Umformtechnik, based in Coburg, Germany, is taking advantage of such servo-electric pump drives in its latest solid and sheet-metal forming presses.
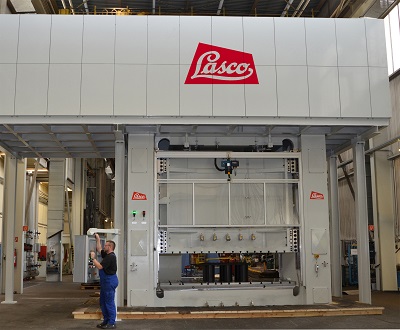
Lasco’s servo-electric pump control for presses uses significantly less energy than conventional valve control systems.
Lasco recently delivered a deep-drawing press supplying 800 tons of force at up to 40 strokes per minute, explained Harald Barnickel, head of the company’s electrical engineering department. At the core of the design is a Simotics 1PH8 servomotor from Siemens, which directly drives a hydraulic pump. Overall control is by a Sinamics S120 drive platform, and a Simotion D445 motion controller handles the complete path, velocity and position control of the axes. The system can rapidly synchronize up to 256 axes and execute precise axis motion and curve profiles, with a response time of just 250 µsec.
“Initial applications have demonstrated that this type of servo technology provides outstanding results,” said Barnickel, and this applies to closed-loop control performance, energy efficiency and overall project success.
The challenge on the deep drawing press was to control force and speed, based on motion profiles set for specific applications. Hydraulic force and, thus, the press force are adjusted via servomotor torque. The motors turn fixed-displacement axial-piston pumps, and motor speed determines the volumetric flow rate and, ultimately, plunger speed.
Four such pump systems connect simultaneously to supply a maximum pressure of 250 bar to the press plunger; three additional pump systems handle the return stroke. “The possibility of scaling, in other words adapting this kind of standard servo solution to the actual requirements, is another advantage of this new technology that certainly cannot be underestimated,” noted Barnickel.
The hydraulic reservoir on the press holds about 2,377 gal (9,000 l). With a flow rate of 16,000 l/min, filling valves control high-speed downward motion of the plunger. Servo pumps supply the required flow for actual pressing operation at speeds to 100 mm/sec. In the past, high-precision control valves with zero overlap were necessary to maintain the precise traversing profiles. Now, the motion control system and servo pumps handle this function, reducing the number of valves by about 40%. The remaining valves are mainly needed to comply with machine safety specifications.
The new set-up eliminates expensive, traditional valve systems and markedly improves energy efficiency, said Barnickel. “In the past, large cooling systems for the hydraulic oil had to be installed. But now, with servo technology, significantly smaller units can be used.” One reason is that the oil is no longer forced through the narrow gaps at control edges of the valves, which eliminates flow-related losses. The press manufacturer is seeing efficiency improvements well into the double-digit range depending on the application, significantly reducing users’ electricity costs, compared to older machines.
Another advantage is that energy can actually be recovered when hydraulic fluid decompresses. This takes place after the pressing operation, and main cylinder pressure must be reduced from 250 bar down to approximately 10 bar before the filling valve to the tank can open. This operation takes approximately 100 msec. Due to hydraulic oil compressibility—approximately 2.5% by volume—and a cylinder volume of approximately 800 liters, the “spring energy” in the oil flows through the axial-piston pump and drives the servomotor. This effect is amplified when relieving the press mechanical system.
In this regenerative operation, the corresponding electrical energy is fed to the dc link of the S120 drive during each cycle. “However, in addition to the energy recovered, the other advantage is that there are no additional power losses in the form of heat, as would be the case with conventional concepts,” Barnickel explained.
Although the Siemens Simotion unit addresses motion-control tasks and can control the complete system, Lasco’s philosophy is to separate the various press tasks. Thus, it uses a fail-safe Simatic S7-319 F 3PN/DP PLC from Siemens as the press-system control, which also allows all safety technology to be implemented without any major additional expense. Fail-safe signals are read via distributed I/O stations and transmitted to the control via Profisafe. This represents a simple yet complete solution, said Barnickel.
Finally, the new servo-electric pump drive for hydraulic presses also improves overall performance, stressed Barnickel. “In addition to the energy savings, its extremely precise controllability is far superior to that of a classic valve control,” he said. Any defined motion profile can be implemented using this concept.
The motion-control system has proven to be extremely valuable in certain steps of the pressing process. For instance, if the plunger moves to upper dead center, then the closed-loop position control in Simotion compensates for any leakage. “A far higher precision is achieved when using servo technology than when using pure valve technology,” Barnickel summarized. The new servo technology for large hydraulic presses has spurred significant interest among Lasco’s customers, he noted. And it is suitable for modernization and retrofit projects.
Siemens Industry
www.usa.siemens.com
Filed Under: News, Pumps & Motors