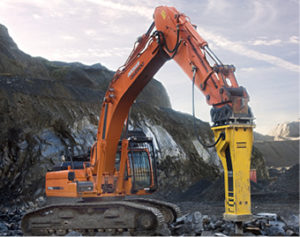
Atlas Copco hydraulic breaker
The once-every-four-years MINExpo show takes place this month and, if you’re a pessimist, the timing couldn’t be worse. The boom-bust cycle in commodities has decimated sales of mining equipment and with it, their hydraulics-intensive systems and all the requisite pumps, valves, cylinders and hose.
Unfortunately, it’s nothing new. Some years ago, I worked as a design engineer for a mining and construction-equipment manufacturer. When times were good, monthly sales ran into the dozens of million-dollar machines. Several hundred engineers, and the hourly workers in our two production plants, were working 55 hours per week. Everyone, it seemed, sported a new car or truck.
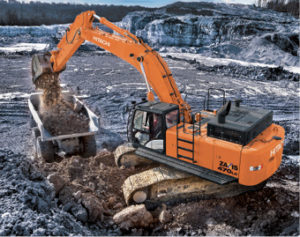
Hitachi ZX 470 LC excavator
Until the inevitable recession hit. Monthly sales dwindled to single digits and eventually, to none at all. Hours were cut and every two weeks another dozen people were trotted down to HR for their layoff notices. Morale was rotten, tensions ran high and we all wondered whose number was up next. When I fortunately found employment elsewhere, head count was down 80%. Eventually the company was forced into a merger that shuttered our facilities and moved all the jobs offshore.
And so it goes today. Caterpillar, which a few years ago acquired Bucyrus International, just announced it will explore “strategic alternatives” for its mining products. That includes halting production of certain equipment, selling off product lines, reducing workforce and repurposing its North Carolina plant from a mining to a rail facility. In July, Komatsu agreed to buy mining-equipment maker Joy Global for about a third of its valuation of only five years ago.
The underlying reasons for current low commodity prices are well documented. According to economist Eli Lustgarten of ESL Consultants, slowing growth in China has put the brakes on commodities demand. As a result, exporters such as Australia and Brazil are faced with excess supplies of raw materials like iron ore and copper. In the U.S., stagnant electricity prices and the EPA’s de facto ban on new coal-fired plants have coal production down significantly.
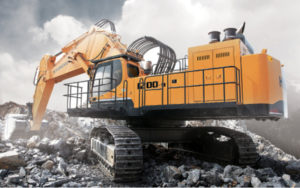
Hyundai R1200-9 excavator
Around the globe, mining firms have scaled back on capital spending or have gone bankrupt. Many companies have postponed normal machine replacement, cut maintenance and, when necessary, cannibalized their existing fleet. For example, mining trucks are normally replaced every 2.5 to 3 years, but that’s now stretched to 6 to 10 years, said Lustgarten. Demand peaked in 2012 at about 1,500 units, and has fallen to around 200 trucks per year today.
The collapse of commodity and energy prices has triggered what Jim Meil of Act Research Co. termed a “death spiral” for mining and oilfield-equipment markets. The good news, he said, is the decline has slowed and is now near bottom. Many experts say population growth and urbanization will drive long-term demand.
Optimists should hark back to the mining-machinery boom of the last decade, when miners complained of equipment shortages and long lead times. MINExpo is as much about future prospects and new technology as it is about current conditions. Around 60,000 people came in 2012. It will be interesting to gage this year’s attendance, and see if better times lie ahead.
Filed Under: Fluid Power World Magazine Articles, Mobile Hydraulic Tips