By Peter Achten, INNAS BV
In “Fluid power genes and memes,” we discussed the essence of fluid power: that fluids are compressible, have viscosity that can vary, and our systems inherently exhibit some internal leakage. And our memes – deep-rooted ideas that aren’t necessarily rooted in fact – such as the perception that hydraulics are inherently inefficient. Now let’s explore two other memes. First, hydraulic systems are expensive and costs can’t be reduced, because production volumes are too small and the number of different applications is endless. And second, that we must accept that our market is too conservative and doesn’t want to innovate.
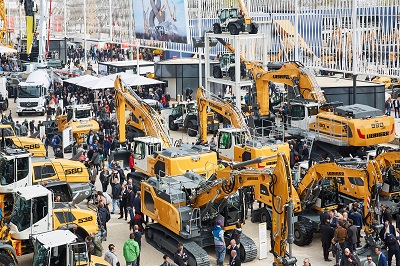
OEMs want more efficient systems that offer better precision and dynamic performance. The fluid power industry needs to adapt, said Peter Achten. (Photo courtesy Messe Muenchen.)
Most engineers aren’t experts on costs. But without economic feasibility, nothing will be accepted by the industry. (Unless you are selling electric vehicles.) Economic decisions are not only about procurement or investment costs, costs are also related to quality. For instance, quality in terms of energy costs.
We think that hydraulic systems are robust, but high friction losses also result in strong wear and high maintenance costs. Troubleshooting is often almost impossible, because many hydraulic systems are so convoluted. And then, finally, our component costs are high, in part because of high labor costs to manufacture these components.
In my career I have visited many hydraulic industries around the world, some very modern, most rather old fashioned. And all of them had one thing in common: high labor costs. Consider a comparison between a gear transmission and a pump. Both are very similar from a construction point of view: Both need a housing, some roller bearings, one or more shafts, and have some highly stressed precision parts. But, despite all these similarities, the gear transmission only costs 13 Euro per kilogram, less than one-third the production cost of a piston pump or motor.
The explanation is in the labor costs. The pump industry has much higher labor costs than the gear-transmission industry or the automotive industry. The hydraulic industry, thus, has an enormous cost-savings potential. But we need new systems and components to harvest this potential. And we also need to create new designs which have less coulomb friction and impact wear, thus reducing maintenance costs.
Further, we need to come up with systems which have a modular design. Modules have the advantage in that they have a clear definition, which allows larger production volumes. And the only way to do this is by having distributed control systems on the basis of a power grid, whether it’s by electric power distribution or hydraulic power distribution. If we do this, we will open up and create enormous market opportunities.
And moving on, perhaps most important meme: the thought that we can’t change. But we have to. If we don’t change, then the world will change us. Darwin didn’t say that the strongest will survive, but the fittest, the one that can adapt to the changing environment.
This year I visited the Hannover Fair and bauma. Everywhere I saw new innovations and new products…but only a few in hydraulics.
Let me give you an example. A pump we recently replaced in one of our test benches turned out to be 50 years old. Now, in 50 years, we have seen many changes. Our phones have been transformed beyond recognition. TV-sets have become ultra-thin, colorful, multimedia, internet devices. Our cars still have four wheels, but that’s about the only thing that hasn’t changed. Washing machines have been revamped, and even baby strollers have been completely redesigned.
When I started to study at the technical university, we made our designs on drafting tables. My first computer programs were written on punch cards. At the university, I started with a simple slide ruler, which was replaced in the second year by a wonderful pocket calculator, which you could even program. My photos were made an analog camera with film that needed to be developed, and I listened to music recorded on cassette tapes. Nothing of this exists today. Everything has been replaced by new products and technologies.
But then our pumps. Other than the color, our replacement pump stayed the same in the past 50 years. It is not that we don’t do anything. There are some promising developments such as independent metering and digital fluid power. I am also pleased that Danfoss has decided to take the digital displacement pumps from Artemis into production, and that Bucher Hydraulics is now producing floating cup pumps and motors.
It is not enough. We need to come with a new plan to do more. We need to focus our research priorities and design new hydraulic systems and components. We have two flavors: systems based on electric power distribution and systems based on hydraulic power distribution. It is absolutely clear that the emphasis should be on reduced power losses, reduced costs, and improved controllability. The market needs and demands efficient accurate and stable control solutions, and especially faster controls.
To fulfill the need for more dynamic systems we have to reduce the amount of oil between the control actuator and the load. This is needed to increase the local stiffness of the hydraulic system. We will need to develop new, efficient components, and avoid valve control as much as possible.
And we have to think again in terms of modules: hydraulic cylinders having their own individual force and position control. This demands the further development of electrohydraulic actuators and hydraulic transformers.
If we can achieve all of this, then we simply will utilize the strength of fluid power.
However, there is a word of caution. The world, our market, is looking for efficient dynamic control. I believe we can play an important role and offer many solutions and meet future demands, but there are some challenges, some caveats to deal with. One of the advantages of valve control is that today’s valve controlled systems have a lot of damping in the system. Once you replace valve control by a more efficient system, you will miss the damping and the systems become much more prone to oscillations.
Furthermore, remember that oil is compressible, and this results in reduced stiffness. And that we have internal leakage that often results in control problems and issues. This is where we have to deal with, this very essence, the genes of fluid power. If we can achieve this renaissance of fluid power technology, then the hydraulic industry has an enormous potential.
The current hydraulic market is a niche market. The pump and motor market has an annual worldwide turnover of around €7 billion. The market of electric motors and generators is much bigger, around €112 billion. The biggest market is currently for mechanical transmissions, having a volume of around €160 billion Euro.
My opinion is not to compete with electric systems, but with mechanical systems. I am convinced that we can have a large part of this market if we can reduce the costs of our systems and components.
So let’s come back to our third topic on our list: the complaint about the lack of willingness to innovate. I don’t care about the question whether the industry is conservative or whether we are traditional. My response to this is rather simple: we can’t stay behind. We can’t afford being conservative or traditional. I care about change and innovation. The question is not if we can change this. No, it’s the certainty that we have to change this.
So where are we? Hydraulic systems have some specific characteristics which make them different from mechanical or electric systems. We have to accept these and use them, if possible, to our benefit. Our future lies in displacement control, in a distributed control system based on modules. This is where we should focus, simply because the market demands it. If we don’t innovate, then the market will find another way without us. We have no choice.
INNAS
www.innas.com
Filed Under: News