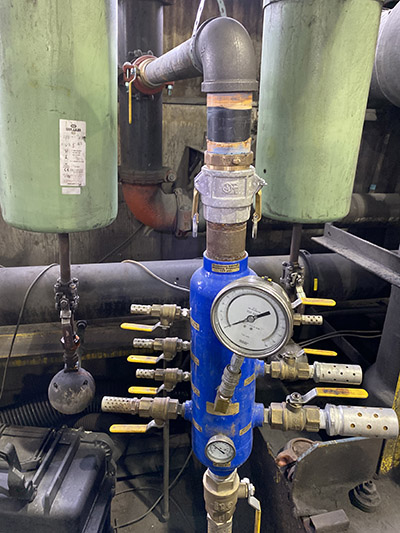
As compressors age, there can be internal wear or control problems that affect the flow output capacity. Often times, observing the amps of the compressor — and comparing that to the motor nameplate — can show if a compressor has problems. If the amps are low, that usually means the compressor flow capacity is lower than rating.
A good way to confirm there are problems is to do an in-situ flow test with a reliable standard. Differential pressure flow meters for wet air (or thermal mass meters for dry air) can be used with good result, but this often means drilling holes in the pipes. Sometimes, there are no suitable piping locations available … or none with enough straight runs to locate a flow meter and have it read accurately.
Years ago, a wise man realized that an apparatus could be fashioned with various sonic nozzles calibrated to flow for use in brute force testing of compressors. All that is required is a suitable sized port, no straight run necessary, and it doesn’t matter if the air is wet or dry. Nozzles are installed with flow calibration of 600, 400, 200, 100, 50, 25, 15, and 10 cfm.
To start, isolate each compressor to operate on the tester and open or close the valves until the pressure is balanced at exactly 100 psi. When the test is over, the nozzles are totaled up and, just like that, you know the capacity of the compressor at site conditions.
A bonus use is that you can open up the isolation valve and allow the compressor to feed plant leaks during non-productive hours. Rebalance the flow tester, subtract one reading from another, and you have your leakage flow!
Filed Under: Components Oil Coolers, Compressed Air Technologies, Engineering Basics, Pneumatic Tips