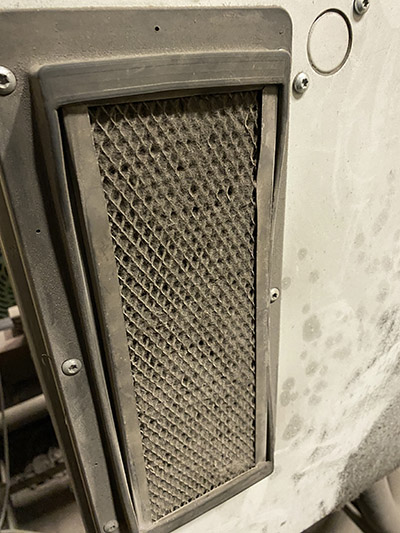
In the compressed air world, the hottest thing in the market lately has been the introduction of variable speed drive controlled compressors. Being hot (as in popular) is good — but being hot as in temperature is not so great. These units, if installed appropriately, can stabilize the air pressure, and save significant amounts of energy … and even pay for themselves in energy savings in only a few short years.
Instead of loading and unloading a compressor, causing a continuously fluctuating sawtooth pressure profile, or using some other inefficient way to match the compressor power to the demand, a variable speed air compressor, if properly applied, will put your system on “cruise control” and maintain system pressure at a constant setpoint. It does so by speeding up and slowing down the compression element (we are talking screw compressors here), continuously varying the output capacity to exactly match the compressed air demand. When this happens, the pressure stays constant (just like setting the cruise control on a vehicle) and the compressor maintains high efficiency.
To vary the speed, some electronic means of control is required. An electronic variable frequency drive will supply the motor, and this drive generates some heat. If the heat within its enclosure is not vented, the drive will fail. Please note that a drive is a complex thing with lots of electronic components, so it needs to be kept as clean and cool as possible. Drive controls installed in very dirty and hot environments will not last very long!
If you do have a VSD compressor, make sure you do regular maintenance on the drive ventilation components and filters. Keep everything as clean as possible. In some cases, locating the compressor to a better location — or remoting the drive — are good solutions that will extend the life of the control and give you trouble free operation.
Filed Under: Compressed Air Technologies, Engineering Basics, Pneumatic Tips