By Josh Cosford, Contributing Editor
In the bustling battlefield of pneumatic systems’ hose and tubing, two contenders stand ready for combat: polyethylene and nylon tubing. Armed with unique strengths and weaknesses, they prepare to face off in the high-pressure war, so let’s dive into this skirmish and see who emerges victorious.
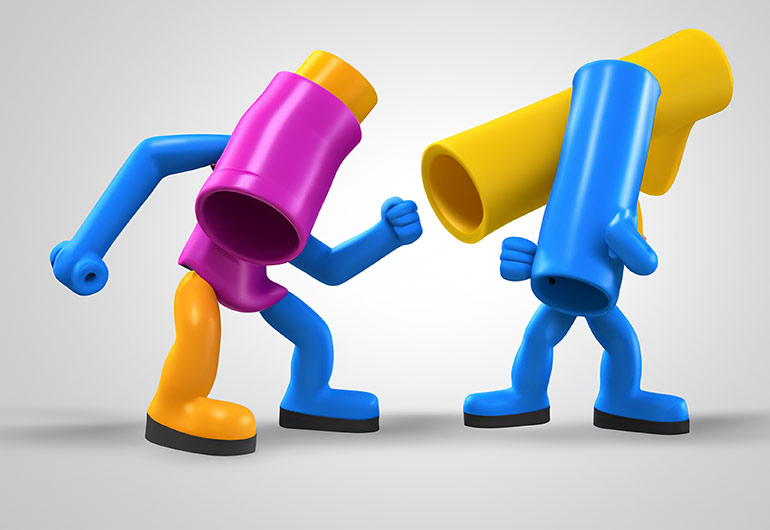
Image generated by AI.
Round 1: The Durability Duel — First to the frontline is polyethylene, often viewed as the scrappy underdog. Polyethylene tubing is known for its flexibility, pliability, and resistance to cracking while offering light weight and impressive chemical resistance. It is a versatile warrior in various pneumatic applications; however, when the going gets tough, polyethylene tubing may falter under some high-pressure conditions.
Enter nylon, the seasoned veteran who comes to the front line with a reputation for high tensile strength and exceptional abrasion resistance. It can withstand higher pressures than polyethylene, standing firm even when the enemy advances. However, this strength comes with a price: nylon is more rigid, making it less maneuverable in tight spaces. The vet might hold the line, but flexibility isn’t its strong suit.
Round 2: The Temperature Tussle — The temperature on the battlefield can make or break even the most battle-hardened warrior. In the sweltering heat or biting cold, performance varies significantly for either side of no-man’s-land. Polyethylene, with its moderate temperature range, can endure the elements to a certain extent, so picture polyethylene as a soldier dressed in BDU (battle dress uniform) for a moderate climate — no “DCU (desert camoflage uniform)” or “snow camo” need apply. Under higher temperatures, it may soften and lose its form, while deep cold could lead to stiffness and poor impact resistance.
Nylon, however, is built to brave the elements and performs admirably across a broader temperature range, from chilly winters to scorching summers. Like a knight with adaptive armor, nylon remains steadfast, maintaining its shape and integrity even under thermal stress. For applications where temperature extremes are the norm, nylon emerges as the victor.
Round 3: The Cost Conflict — In the war of the wallets, cost-effectiveness can be a decisive factor that can turn the tide of war. Polyethylene, the budget-friendly combatant, offers a cost advantage while remaining effective and economical for many tasks. PE tubing provides good value, making it a popular choice for budget-conscious operations where high pressure isn’t a critical concern.
On the other hand, nylon demands a higher price because of its superior qualities. Think of it as hiring elite special forces — more costly but offering exceptional performance and durability. For applications where pressure resilience and longevity are paramount, the extra investment in nylon can pay off in the long run.
The Victor: Strategic Superiority — In the grand scheme of pneumatic warfare, the victor depends on the battlefield conditions. For applications where flexibility, chemical resistance, and cost-effectiveness are key, polyethylene stands as a worthy contender. It’s the go-to choice for less demanding environments, performing admirably without breaking the bank.
However, when high-pressure resilience, temperature extremes, and durability are the call of duty, nylon tubing takes the win in this battle. Its robust construction and steadfast performance under harsh conditions make it the ultimate champion in the pressure war. Keep all these things in mind when choosing between polyethylene and nylon tubing.
Filed Under: Components Oil Coolers, Engineering Basics, Featured, Hose Assembly Tips, Technologies, Tube & Hose