Hydraulic piston pumps are the current standard for power, control and efficiency, but such a position in the hierarchy comes with more significant investment and responsibility. Piston pumps are expensive, complicated and involved compared to their lessor counterparts, such as the venerable gear pump. Inexpensive piston pumps still start in the four-figure range, and once you have them, you must understand how to set up one of various control devices such as pressure control, load sensing or remote control. All control devices require different procedures to commission, so qualified technicians only need apply.
A gear pump costs a tenth the investment of a piston pump, but aside from the apparent deficiency in efficiency, can we power up our hydraulic accoutrement to mimic the capability of a pressure-compensated pump? You bet. Load-sensing piston pumps read pressure signals downstream of each variable orifice — such as proportional valves or lever valves, for example — and then regulate the pump at a standby pressure equal to the desired pressure drop across the valves.
Using check or shuttle valves connected in parallel, the pump compares the last pressure signal at each work port to the pressure at its outlet and adjusts the compensator to offer just enough pressure and flow to suit the machine’s demands on top of standby pressure. From my observation, a typical standby pressure is 300 psi, but the controller offers an adjustable screw for setting your desired pressure.
I’m sure you’re wondering how we can modify a gear pump to vary its pressure and flow to suit the demands of individual actuators and their demands. Look not at the gear pump but rather how we control the downstream functions. The selection of cartridge valves available today is mind-boggling, and one trick is using a type of pressure-compensating, load-sensing valve that automatically directs excess flow to tank at a value matching its spring pressure. Functionally, the circuit operates much like a load sense circuit on a pump to ensure that only enough pressure and flow as needed are directed at the actuators.
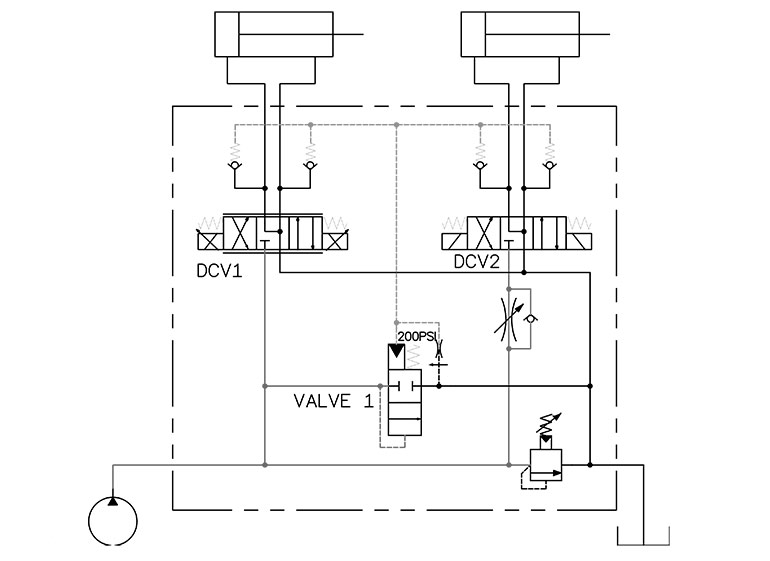
Figure 1. A sample circuit using load-sensing pressure compensators
My example in Figure 1 shows such a sample circuit drawing in its cleanest form as a custom integrated manifold installed with cartridge valves. I’ve used just two directional valves and actuators for simplicity, and the load-sensing compensator is Valve 1 near the relief valve. The pilot port accepts the load sense signal, which you can see daisy-chained from the check valves connected to the work ports after the valve. These pilot locations are essential because the compensator must observe pressure after all the combined valves and orifices to best meter flow to suit what you’re asking of the actuators.
The valve DCV 1 is a proportional valve which varies its flow based on a signal from the electronic controller, and any flow above and beyond what’s being asked of the valve will be directed to tank by the compensator. The flow through the proportional valve will be affected by the bias spring of the pressure compensator, in this case, 200 psi. Just to clarify, the circuit will sense the pressure past the directional valves (the orange pilot lines), compare it to system pressure (red lines) and then allow 200 psi pressure drop through the DCV 1.
DCV 2 is a simple “bang bang” valve that is fully open or closed when actuated. The compensator will dump all pump flow to tank when both valves are closed, but when DCV 2 opens, it will flow equal to the combined pressure drop across the needle valve and itself. As expected, all other flow is directed to the reservoir.
So, is this setup mirroring a load-sensing piston pump? Close, but not really — it’s still a flow-sensing circuit, but with a critical difference. It allows for the functionality of the control circuit and the easy method to dump a fixed pump’s fluid to tank at low pressure when functions are idle. However, it has one downside — you still can’t sidestep the fixed flow nature of the gear pump. It’s constantly flowing, and in any circumstance you’re using partial flow (through DCV 1, for example), the remaining flow dumps to tank at the current system work pressure. As you’ll remember, any pressure and flow lost before doing work is manifested as pure heat. This isn’t a knock to the load sense compensator so much as it is to constant flow systems.
Regardless, if your machine and its circuit are limited to a gear pump but require more sophisticated control circuitry, explore the many possible options using load-sensing pressure compensators. Although pressure-compensated pumps are fantastic and have their place, there’s something satisfying about coming in way under budget.
Filed Under: Components Oil Coolers, Engineering Basics, Pumps & Motors, Valves & Manifolds