The right lubricants can improve profitability, productivity and sustainability.
Contributed by Blayne McKenzie, Strategic Technology Manager, Industrial Products, The Lubrizol Corp.
Procurement decisions in almost any market you can imagine are driven primarily by one or more of the following three factors: profitability, productivity and sustainability. In the rapidly evolving world of hydraulic equipment, hardware is changing quickly to meet demands for more throughput on both mobile and stationary equipment. This requires each system component to operate under ever more challenging circumstances. But it is not just the hardware that is changing — hydraulic lubricants must also change in lockstep with the hardware. After all, the evolving equipment is operating at higher operational speeds and pressures, increasing use of electronic control, greater precision and accuracy, and more compact systems that demand smaller lubricant sump capacity.
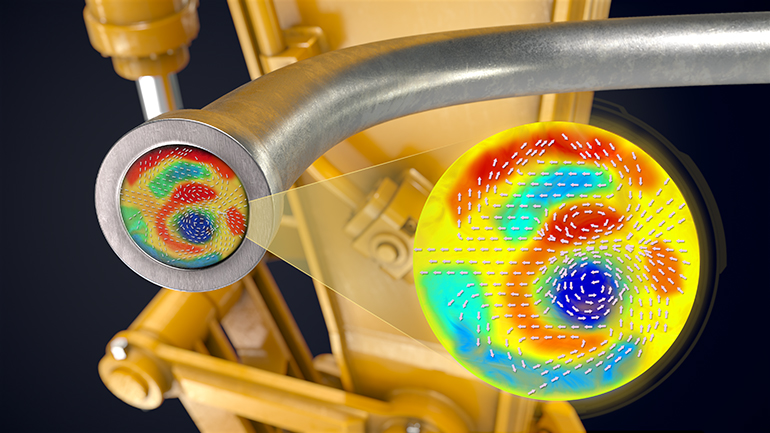
In light of the rapidly changing equipment requirements, one thing remains constant: Facilities cannot afford the effects on profitability of unplanned downtime. To prevent that from happening, lubricants also must not fail. Lubrizol’s research has focused on creating a total hydraulic solution by combining industry-known, durable additive chemistry with shear-stable, energy-efficient polymers. This combination of chemistries improves profitability through reduced fuel and energy costs; productivity by keeping equipment in working order more consistently; and sustainability by reducing energy consumption and carbon dioxide emissions—all while maximizing lubricant durability.
Passing the test
No lubricant can enter the market without passing a series of standardized bench and OEM hardware tests. Having accomplished both of those milestones, Lubrizol 5703 has established itself as a well-known additive package. Then Lubrizol’s hydraulic fluid development team combined it with a specially designed performance polymer called Lucant, which helped maintain durability in the Eaton 35VQ vane pump test. The end-of-test weight loss measurement clearly stays within the published test limit (Figure 2).
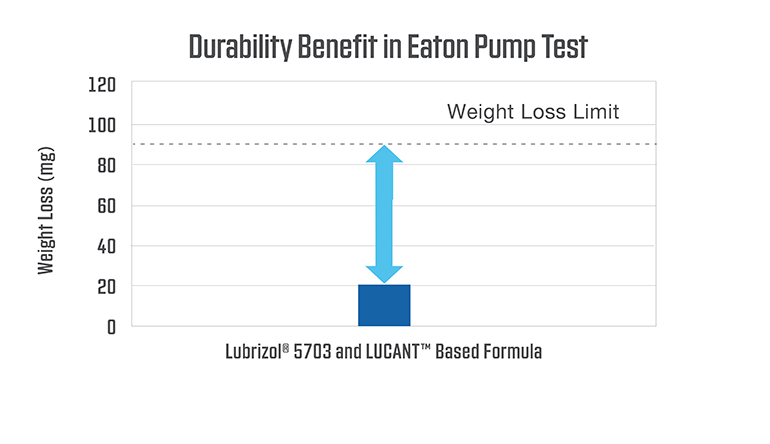
In addition to providing critical wear protection, Lubrizol’s hydraulic energy-efficient offering also delivers lower operating temperatures by up to 17% in industry pump rig testing. This additional benefit is a consequence of reduced fluid friction, or traction, delivered by the Lucant line of performance polymers.
We have evaluated the traction coefficient of a commercially available HF-0 approved multigrade fluid and compared its frictional properties to Lubrizol’s efficient HV (multigrade) solution. By deploying molecules known to reduce fluid friction, in this example by as much as 9%, reduced operating temperatures and greater fluid flow through the network of pipes and bends of a hydraulic system can be realized.
With cooler-running hydraulic systems comes related oil-drain life-increasing performance. One indicator of the real-world ramifications of reduced operating temperature is the generation of oxidation products, such as sludge. Lubrizol’s enhanced thermal stability performance reduced sludge. In an industry-standard sludge test, a 96% reduction in sludge was observed, offering another example of extended oil life and system durability.
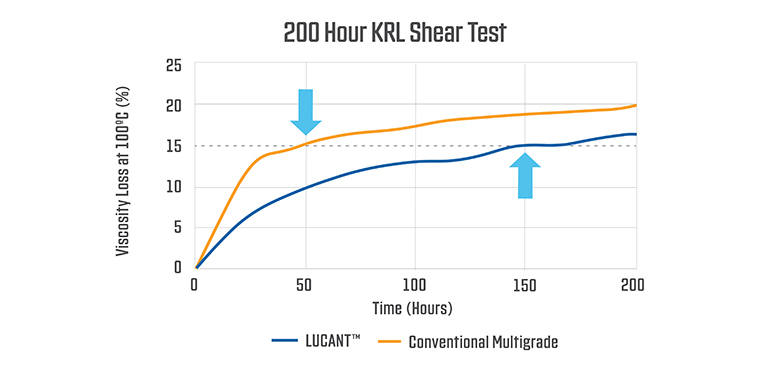
As companies decide whether to change from a monograde hydraulic fluid to a multigrade one, they must consider the stay-in-grade shear stability of the viscosity modifier. In the case of Lucant, that means it not only maintains appropriate multigrade, low-temperature performance while staying durable, but it also offers more protection than more conventional multigrade viscosity modifiers. In Figure 3, the 200-hour KRL bearing shear test data proves the improved shear performance of Lubrizol’s total hydraulic solution. As can be seen, it stayed well below the 15% viscosity loss threshold three times longer than a conventional multigrade hydraulic lubricant.
Saving energy saves money
To confirm and quantify the energy savings, Lubrizol authorized real-world field trials. Using an off-highway wheel loader, a mobile field trial showed diesel fuel savings of 1.4% to 2.7% depending on when and where it was used, as well as the ambient temperature of the air (Figure 4). It also tested its combined fluid in a stationary hydraulic injection molding machine, where the Lucant-containing lubricant showed an 8.5% reduction in electricity consumption (Figure 5).
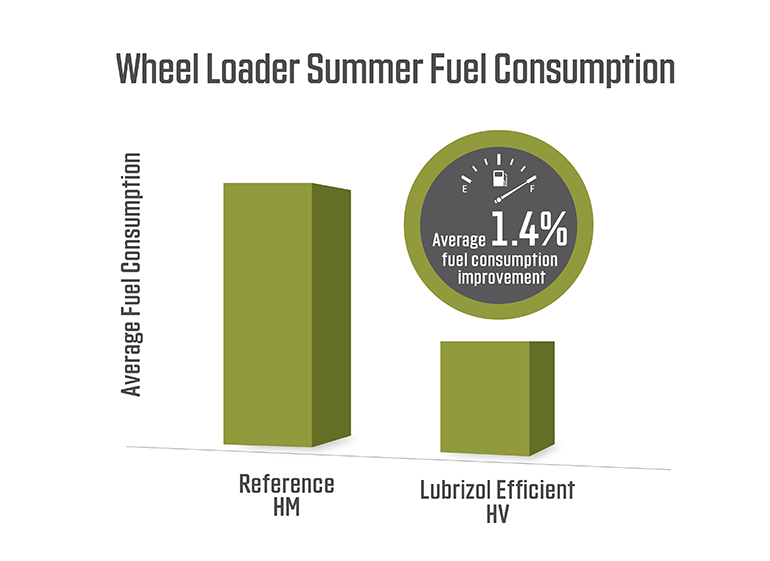
Confirmation comes in the lab
Though the field trial results were certainly promising, confirmation from lab results were in order. Lubrizol’s hydraulic fluid development team set out to run other experiments in a controlled lab environment, specifically to eliminate the constraints and variables inherent to field testing. To that end, the team created Lubrizol’s Total Hydraulic System Efficiency Rig, which did just that. Originally designed to imitate a real-world skid steer, the rig also contains the essential elements of a hydraulic system. In addition to hydraulic pipes, hoses, and valves, the rig incorporates an off-the-shelf commercial piston pump that supplies a hydraulic circuit. In addition, the rig can be configured in different ways because of its modular design, which allows for more extensive testing than can be done in field tests. Efficiency testing, done over the prescribed condition set, was designed to capture the diverse duty cycles and system requirements of a skid steer.
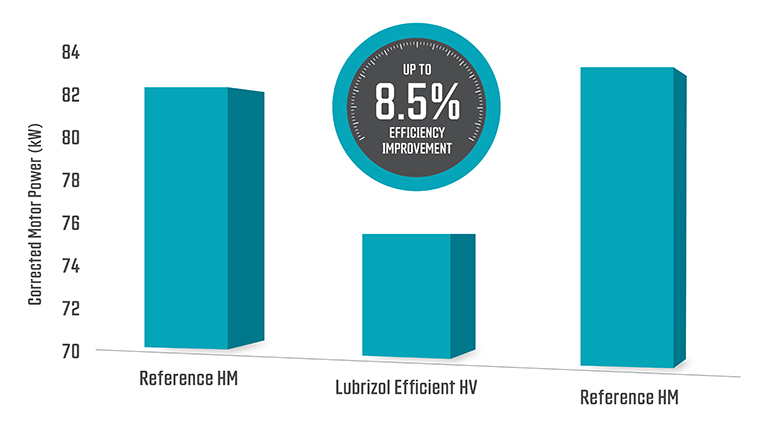
The rig was provided a significant number of flow, pressure, and temperature sensors, which allowed researchers to do exhaustive future-looking hydraulic efficiency research. First, however, it was used to corroborate the efficiency gains seen in the field with the use of Lucant and Lubrizol 5703. In Figure 6, it can be seen that the Lucant fluid improved efficiencies over both a monograde (3.8% better) and a conventional multigrade lubricant (1.6% better).
How does it work?
Lubrizol 5703, combined with the Lucant performance polymer, provides substantial efficiency gains both in the field and in the lab, but at a molecular level, what is its mode of action? Lubrizol, in partnership with university researchers, discovered that it presents unusual performance benefits that are not available in other more conventional hydraulic viscosity modifiers. As a result of its distinct molecular structure, Lucant lowers the number of parasitic losses that occur when fluid flows around bends, twists and turns, or through valves, filters and other nonlinear hardware flow paths. Figure 1 illustrates a secondary flow field (denoted by the arrows) as a fluid navigates a 90° bend.
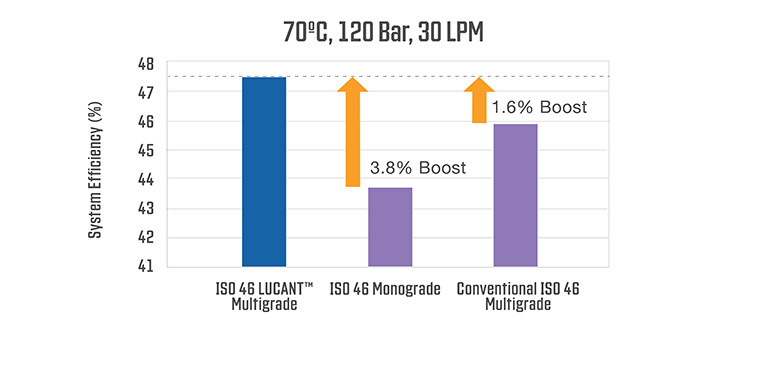
While conventional hydraulic viscosity modifiers do not always reduce the intensity of these secondary flow vortices effectively, Lucant can and does by forming small, flexible chains with respect to their overall contour length. Its large extensibility parameter provides viscoelastic behavior. In contrast, conventional viscosity modifiers contain long sidechains and short backbones to prevent tight coiling and reduce flexibility. Those characteristics reduce their extensibility and provide no detectable viscoelastic effect. Lucant’s viscoelastic chains accumulate and remove energy from the coherent vortices, which lead to their decay.
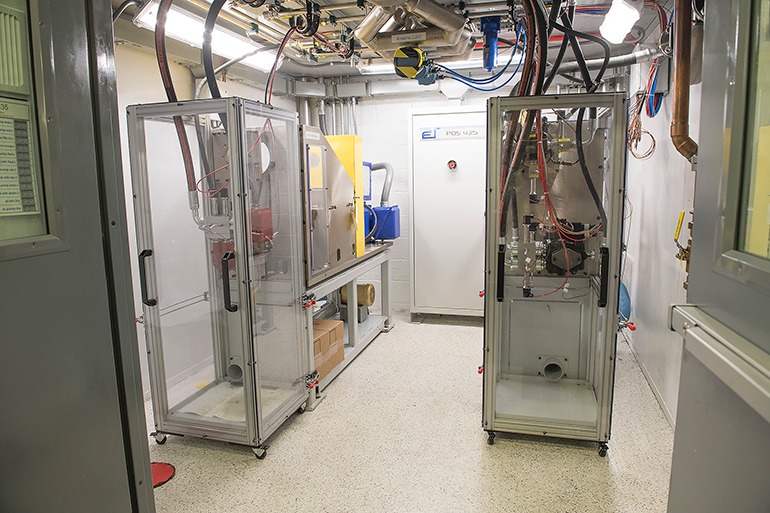
Reducing fuel consumption is the key to saving money over the long term, and Lubrizol’s total hydraulic solution helps reach those monetary goals through reduced fuel consumption in mobile equipment and electricity savings in stationary systems. That is not the only savings it produces, however — it can also help save the Earth. Using a total hydraulic solution can combat climate change by reducing carbon dioxide and resource consumption, thereby improving the environment for future generations and promoting greater sustainability within the lubricant industry itself.
Lubrizol
Lubrizol.com
Filed Under: Filtration/Contamination Control, Sealing & Contamination Control Tips