By Josh Cosford, Contributing Editor
Hydraulic hoses are critical components of any hydraulic system, and their lifespan is essential for its efficiency and longevity. Several factors impact hydraulic hose life, from environmental conditions to maintenance practices, and if you heed the impulse testing tips below, you can enjoy long life from your machine’s hydraulic hoses.
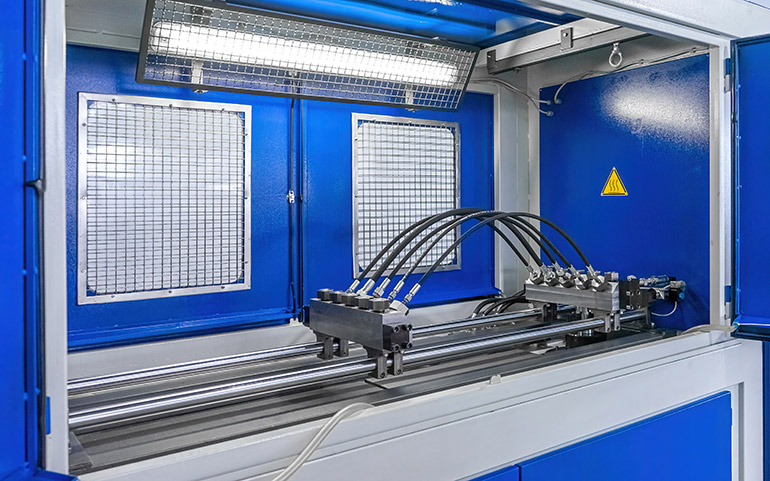
Ensuring that hoses undergo impulse testing is one of the most crucial steps in evaluating their reliability and durability. Impulse testing involves subjecting the hydraulic hose to repeated pressure cycles, simulating real-world operating conditions of pressure spikes and machine cycles. This test evaluates the hose’s ability to withstand those pressure spikes, pulsations, and pressure reversals, which are common occurrences in hydraulic systems. By conducting impulse testing, manufacturers and users can gain valuable insights into the hose’s performance under stressful conditions, helping them select the most suitable hose for a specific application.
Impulse testing serves several essential purposes:
Quality assurance: Impulse testing is a vital part of quality control during the manufacturing process. It helps identify any weaknesses or defects in the hose’s construction before it is released for use. Manufacturers can ensure that their hoses meet or exceed the required performance specifications by adhering to industry standards and performing rigorous impulse testing.
Performance validation: Hydraulic systems often encounter sudden pressure surges and fluctuations during operation, which is sometimes predictable (presses) but sometimes unpredictable (mobile machinery). Impulse testing assesses how well the hose can handle these pressure variations over time. A hose that can endure repetitive pressure cycles without failure ensures a more reliable and longer-lasting hydraulic system (since any old hose will handle steady working pressure indefinitely).
Safety and reliability: A hydraulic system failure can lead to catastrophic consequences, including damage to machinery, downtime, and even injury to personnel. Impulse testing helps ensure that hoses are safe and reliable, reducing the risk of accidents and system failures.
Predictive maintenance: Impulse testing data can provide valuable insights into the hose’s expected lifespan and potential failure points (including recent advancements in IoT technology). This information allows maintenance teams to schedule preventive maintenance and replacement, reducing unplanned downtime and overall maintenance costs.
Product development and improvement: Impulse testing also plays a role in the continuous improvement of hydraulic hoses. Feedback from testing can lead to design enhancements, material improvements, and innovative solutions to make hoses more robust and efficient.
Although not as common as it should be, impulse testing is paramount for hydraulic hose assemblies and the machines they plumb. It is an essential tool in ensuring hose quality, safety, and reliability. By subjecting hoses to rigorous impulse testing, manufacturers and users can gain confidence in their performance under real-world conditions, leading to longer-lasting hydraulic systems and reduced operational risks. Properly designed systems, regular maintenance, and selecting the suitable hose for the job, combined with impulse testing, are critical factors in extending hose life and ensuring hydraulic system efficiency and longevity.
Filed Under: Engineering Basics, Hose & Tubing, Hose Assembly Tips