Imagine you’re in charge of automating a factory or warehouse. You need to move products quickly and efficiently from one point to another and consider pneumatics as a solution. Pneumatic systems need plumbing, lots of it. The most popular plumbing conduit for air systems is synthetic plastic or rubber tubing or hose. However, with so many types of pneumatic hose available, how do you choose the best one for your application? Let’s start by looking at the factors you should consider when selecting a pneumatic hose.
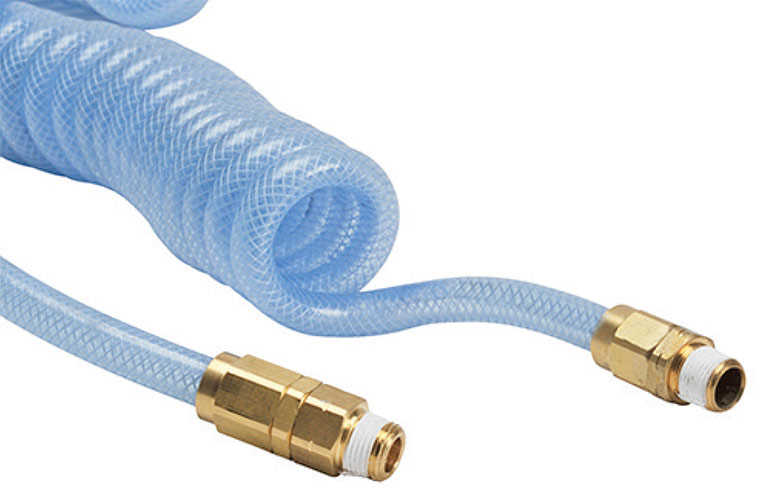
Image courtesy of AutomationDirect
Firstly, you need to consider the flow rate of your components and actuators and, therefore, the pneumatic hose. For example, if you have high-volume production lines or need to move large actuators quickly, you’ll need a pneumatic tubing with a high flow rate to ensure you provide your machines with the flow they need to do the job.
Secondly, you need to consider material composition because it plays a part in flexibility, durability, weight, and compatibility with external factors. The chosen tubing material is crucial for food and beverage applications, where you need to use food-safe compounds that will not leave toxic residue. For example, you don’t want to use pneumatic tubing that could contaminate your food or beverage products, which is the case with PVC, which is not recommended.
Polyurethane hose is widely used in automation and robotics applications due to its high flexibility, durability, and resistance to abrasion, chemicals, and UV rays. It is also suitable for use with compressed air systems and in the food and beverage industry (think CO2 lines for soft drinks).
Nylon tubing is commonly used in pneumatic systems for its high resistance to pressure, excellent flexibility, and solid durability. But, again, it is also suitable for use in compressed air systems and the food and beverage industry (think CO2 lines for beer).
Polyethylene material is excellent for various pneumatic applications due to its flexibility, low weight, and resistance to chemicals and impact. Teflon is a plastic unmatched for high-temperature applications and in environments where chemicals are present due to its high resistance to both. They are commonly used in the chemical, pharmaceutical, and food and beverage industries.
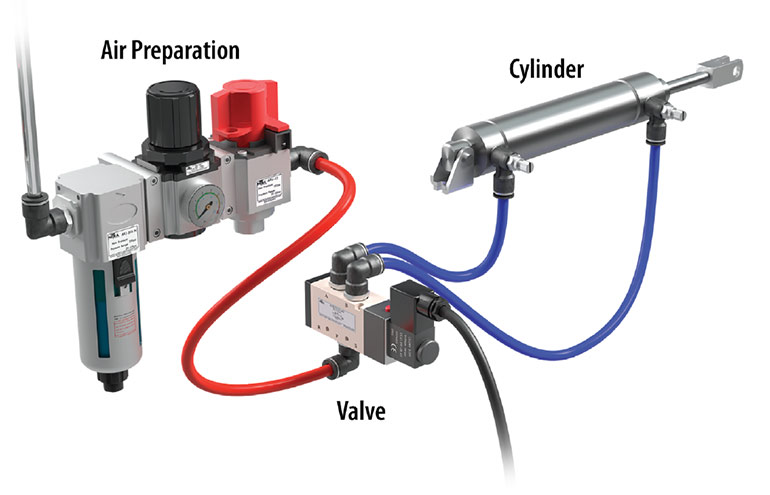
Image courtesy of AutomationDirect
Thirdly, you need to consider the pressure rating of the pneumatic hose. Not all tubing provides the same pressure-resisting capacity, especially in more exotic applications that are hot, cold, or exposed to ambient chemicals. In addition, tubing is rated with consideration to a safety factor, so be sure to select the hose for its working pressure rather than its maximum pressure.
Fourthly, you need to consider the size and length of the pneumatic tubing. Longer tube will have more cumulative pressure drop, so you may need to choose a larger size to accommodate. Also, consider if the hose is stationary or moves frequency, such as in cable carriers. A rigid hose such as Teflon might not last as long as a more flexible choice such as nylon.
Finally, you should balance the previous considerations with cost. Pneumatic tubing is available at a range of price points, and you need to select one that fits within your budget but still meets your needs. Many fluid power distributors will offer bulk discounts for purchasing rolls of tubing rather than smaller sections. If your shop builds a lot of equipment, you’re likely color-coding your tubing. Although no industry standards exist for air lines, it is common to use red for pressure and blue for atmosphere.
Filed Under: Components Oil Coolers, Engineering Basics, Hose & Tubing, Hose Assembly Tips