Parker Hannifin showcased a variety of technologies at IFPE 2023. The booth featured new and evolved products in their smart electrification technology portfolio aimed at enabling battery-powered machines. Though Parker is known for hydraulics, the company has been creating electric components and integrating hydraulics into electric systems for almost 40 years.
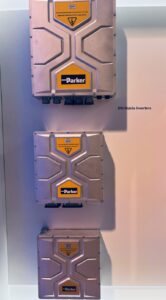
Parker’s next-generation high-voltage inverters integrate functional safety for traction and pump control applications.
At IFPE, Parker displayed its next-generation inverter with built-in functional safety. The Global Vehicle Inverter (GVI) uses the same hardware with two different software configurations to provide traction control or hydraulic work functions.
The GVI inverter can control an EHP Series Configured ePump, which consists of a Global Vehicle Motor (GVM) directly coupled to a hydraulic pump.
“The GVM is a permanent magnet AC motor with a power-dense design and an integral cooling tube built into the core diameter of the motor. In many cases, you have to put a bulky jacket around the motor. But since we have the cooling tubes inside the motor stator, we can get a lot of power out of a very small piece of equipment,” said Christopher Griffin, business development manager for electrification at Parker.
Based on experience and mobile application requirements, Parker released the EHP Series Configured ePumps to help machine designers select the right motor-pump combinations for hybrid electric mobile work functions and auxiliary applications. The combinations include:
- GVM Electric Motor and P1M Piston Pump
- GVM Electric Motor and T7 Vane Pump
- GVM Electric Motor and F11/F12 Bent Axis Pump
- GVM Electric Motor and PGP Gear Pump
“They all have their uses. Some are efficient, some are quiet, some are less expensive — it really depends on the machine builder’s needs,” said Griffin.
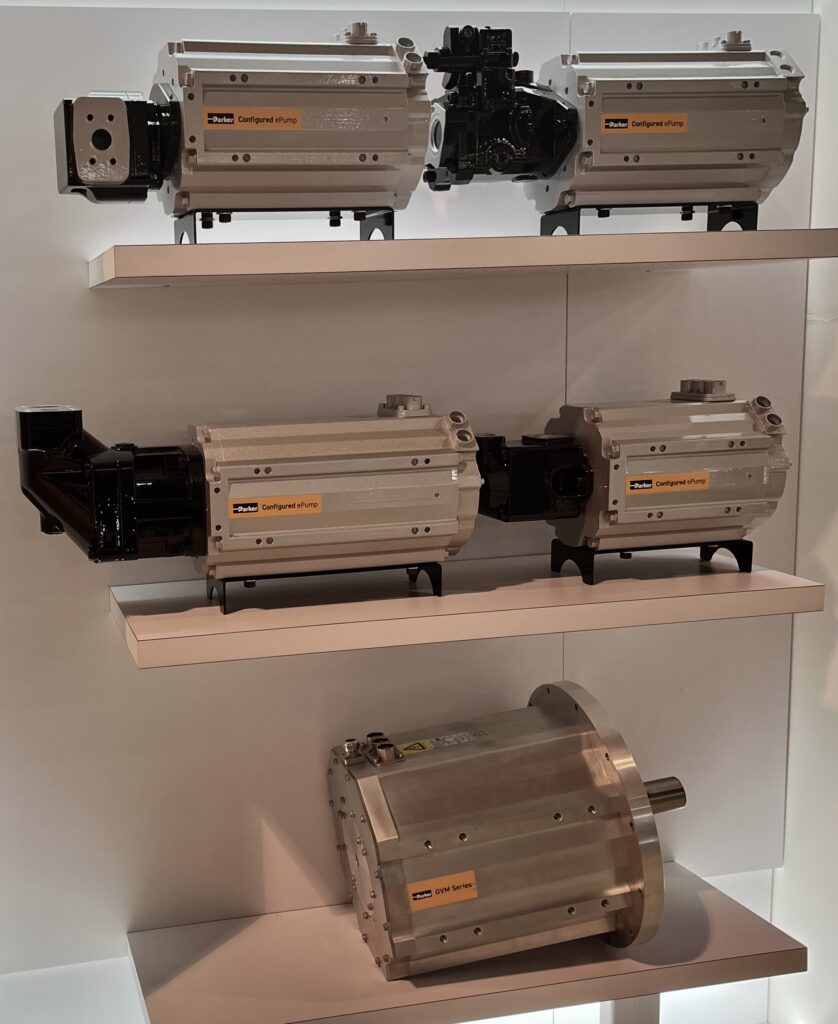
Parker’s EHP Series Configured ePumps include a GVM electric motor and hydraulic pump.
The booth also had an example ePTO to show how a GVI inverter and EHP Configured ePump could be configured for a truck chassis. The assembly had a two-stage pump and a coolant system with components designed specifically for electric vehicles.
“Now, hydraulics aren’t going away,” said Griffin. “They’re too good at what they do, and we’re not suggesting they should go away. But we can do things to make them more efficient. For instance, the simplest way is to drive all the hydraulics off one motor or start to decentralize the hydraulic functions so that multiple motors only produce power when needed rather than idling. But that comes at a cost penalty and potentially a weight penalty. It just depends on the machine and what the machine builder wants to achieve. It could be cost, weight, the number of workday hours you can reliably get — in any case, there are ways to make the system more efficient.”
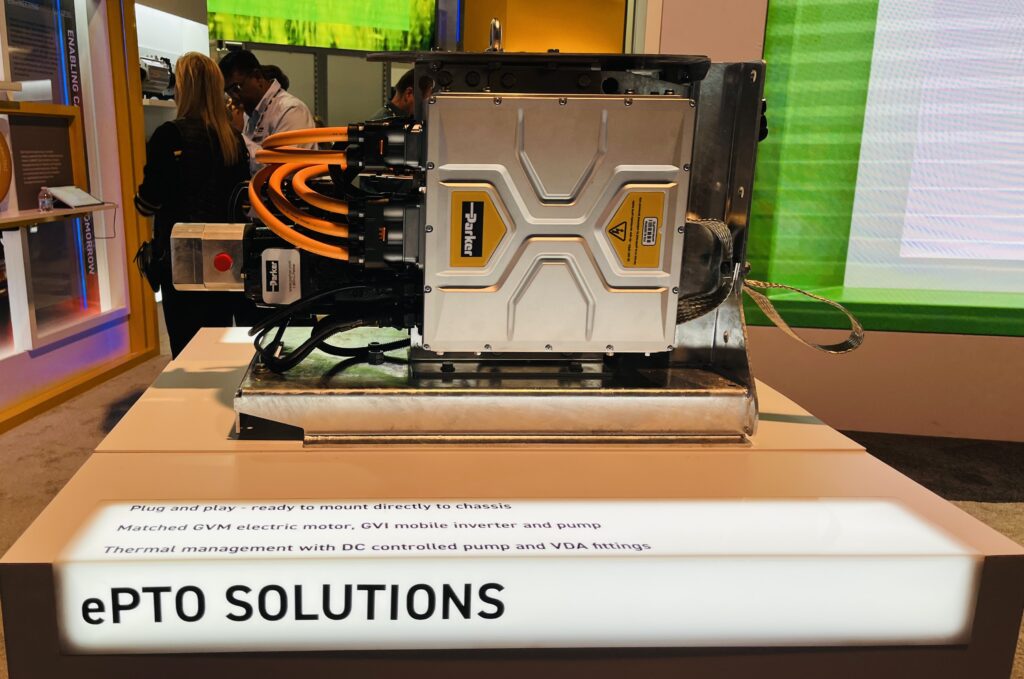
Shown here is an example of an ePTO configured for a truck chassis. The system consists of a GVI inverter, EHP Series Configured ePump, and a coolant system.
Parker also showcased its latest Critical Protection hose cover for abrasion and impact resistance in harsh environments, such as mining, construction, and refuse.
“One of the main failures occurs when objects crush the outside cover of the hose, so we created an unbreakable cover with abrasion resistance,” said Sterling McNeill, business development manager for the fluid connectors group at Parker. “If a hose bursts deep within an underground mine, they have to stop everything and manage the environmental impacts. Now they don’t have to worry how far they are underground.”
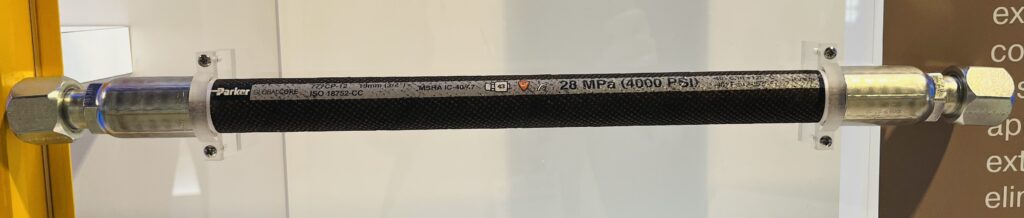
Parker’s Critical Protection hose cover is designed for abrasion and impact resistance in extremely harsh environments such as underground mining.
The CP cover complements the ToughCover (TC) and SuperTough (ST), providing different levels and types of protection.
Parker Hannifin
parker.com
Filed Under: Hose & Tubing, Mobile Hydraulic Tips, News, Pumps & Motors