By Josh Cosford, Contributing Editor
Pneumatic systems are common in various industries, including automation, food & beverage, and packaging. They’re preferred over other systems for their simplicity, efficiency, cleanliness and versatility. Pneumatic systems rely on hoses to transport compressed air from the compressor to the devices that use it. There are many types of hose, each with unique properties and applications.
However, pneumatic hoses are prone to failure over time, like any other mechanical component. Therefore, it’s essential to understand the types of failures that may occur and how to prevent them. Here are some of the most common types of pneumatic tube failure and how to prevent them.
One of the most common types of pneumatic tube failure is abrasion. Abrasion occurs when the hose rubs against another surface, causing it to wear out over time. Abrasion also occurs from friction between the hose and other components, such as fittings or the machinery itself. To prevent abrasion, consider using abrasion-resistant hose, protective sleeves, or installing the hose in a way that reduces contact with other components.
Kinking occurs when a hose bends too sharply, causing it to collapse or form a permanent bend. In addition, kinking can restrict airflow or damage the hose, leading to a loss of pressure as it leaks. To prevent kinking, install the hose correctly, with gradual bends and no sharp angles. All tubes have a minimum bending diameter, and any bends tighter than recommended could lead to a kink. If the hose needs to bend sharply, consider using a female-to-female elbow or installing a swivel joint.
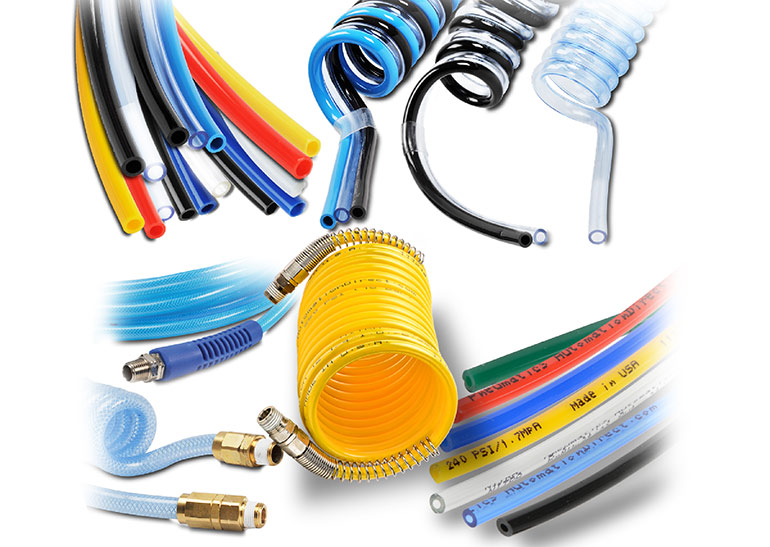
When a hose is compressed or flattened, either by vacuum or by the weight of other components, the result is a crushed hose. Crushing can damage the hose, restrict airflow, or cause leaks when repeated events eventually lead to fatigue. To prevent crushing, ensure that the hose is installed in a way that reduces contact with heavy components, such as machinery or vehicles. For example, consider using a protective sleeve or routing the hose to reduce external pressure.
Chemical damage occurs when a hose is exposed to chemicals that degrade its polymer. This can cause the hose to weaken, crack, or become brittle, leading to leaks or failure. To prevent chemical damage, consider using hose resistant to the specific chemicals in your environment. If the hose must be exposed to chemicals, ensure it is cleaned and maintained regularly.
Aging is a reality for pneumatic tube and occurs when a hose degrades over time due to exposure to sunlight, heat, or moisture. Aging causes the hose to become brittle, lose elasticity, or crack, leading to leaks or failure. To prevent aging, consider using hoses designed for outdoor use or with UV-resistant properties. Store hoses in a cool, dry place and avoid exposure to direct sunlight or heat sources.
Understanding the types of pneumatic tube failure and how to prevent them is crucial to maintaining the efficiency and reliability of your pneumatic system. By choosing the appropriate type of hose, installing it correctly, and performing regular maintenance, you can minimize the risk of failure and ensure optimal performance. In addition, regular inspection, testing, and replacement of worn-out hoses will help you catch potential failures before they occur, saving you time, money, and effort in the long run.
Filed Under: Components Oil Coolers, Engineering Basics, Hose & Tubing, Hose Assembly Tips