Risks versus rewards of complete hydraulic drive maintenance practices
Contributed by Timothy McCrea, market segment manager, aftermarket, pulp & paper, Hägglunds – Bosch Rexroth Corp.
Hydraulic direct drive systems are a crucial part of industrial recycling operations. Engineered for reliable performance under demanding conditions, recyclers and other users of these systems will sometimes postpone critical maintenance practices because the drives are so rugged and reliable.
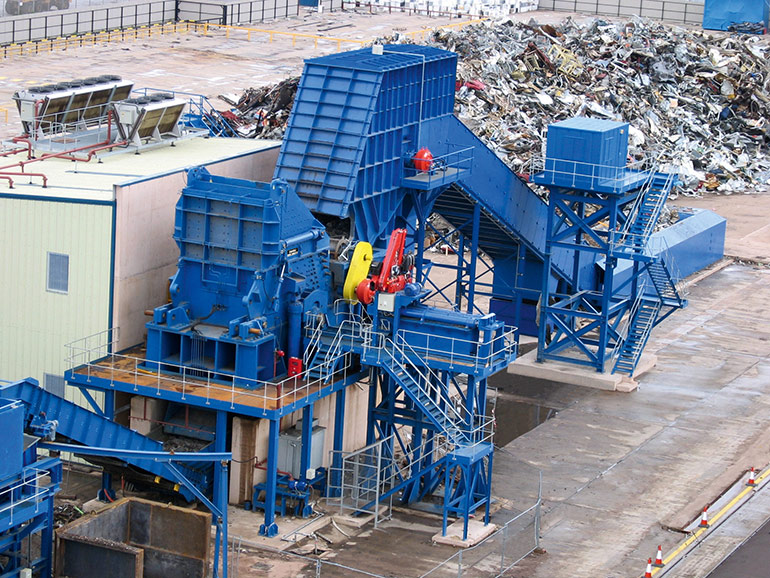
Complex recycling operations rely on the reliability of hydraulic direct drives.
The risk: Even the best hydraulic systems can have problems that can lead to reduced energy efficiency, increased safety incidents and, ultimately, “breakdown maintenance” with costly unscheduled downtime. Avoid the risks of breakdown maintenance and reap the rewards by incorporating these drive maintenance best practices into your operations.
1. Periodic maintenance checks
Risk: Expensive and disruptive downtime
Emergency repairs are often more difficult and costly to make. When small problems or malfunctions persist, they can become major failures requiring drive removal and shipping to repair centers, potentially taking a vital shredder or other major piece of equipment offline.
Reward: Increased uptime and cost control
Best practice is to implement monthly hydraulic equipment inspections — and make sure they aren’t skipped. These can prevent minor issues from becoming major problems. Document danger signs, such as main pump pressure changes or fluctuations in motor speeds, and then schedule further service work if the issues persist.
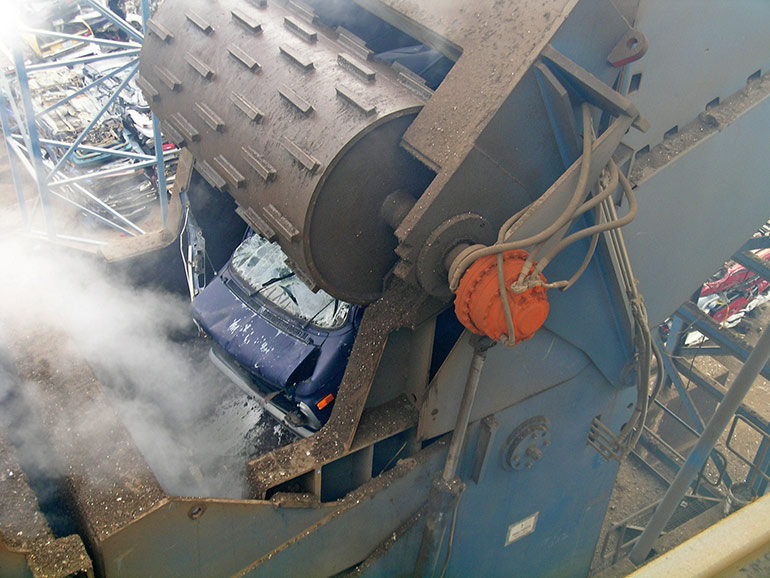
Hydraulic direct drives are rugged and reliable in the toughest environments but consistent, proactive maintenance ensures uptime.
2. Fluid selection and condition
Risk: Poor equipment performance
Substituting the wrong hydraulic fluid instead of the fluid specified by the drive manufacturer can lead to less efficient drive performance. Equipment like infeed conveyors, double feed rolls, scrap shears and baling presses are exposed to contaminants like high dust levels or metal shards that can contaminate fluids and ultimately damage hydraulic motor components.
Reward: Protection from equipment damage
Follow the manufacturer’s recommended fluid viscosity ratings and consider environmental factors, such as high-temperature conditions. Regularly monitor hydraulic fluid for contaminants, particles or discoloration; degrading oil condition is a critical warning sign that motor components can be worn or damaged.
3. Service filters and seals
Risk: Contaminant damage
Based on an environment’s dust and contaminants, drive manufacturers provide filter specifications and replacement intervals. Using alternative filters or skipping filter replacement, especially on equipment like shredders or conveyors that undergo high levels of shock loading, risks fluid contamination and damage to drive components.
Reward: Smoothly operating drives
Following all the manufacturer’s recommendations on filter selection and replacement is the best way to maintain the long-term health and performance of drive hydraulic fluid. In addition, check O-ring seals for signs of leakage that may indicate seals are wearing out due to shock loading and vibration, and schedule O-ring replacement and tightening of fittings.
4. Use OEM-sourced parts
Risk: Breakdowns due to “remanufactured” parts
Some repair shops will repair hydraulic direct drives with used parts taken from scrapped motors or from third-party aftermarket suppliers. Use of these parts cannot provide the same guaranteed level of reliable performance under high shock load conditions that are provided by the manufacturer’s supplied replacement parts.
Reward: Confidence in “like-new” performance
When repairing hydraulic direct drives, using original parts manufactured to the manufacturers specifications is the surest way to return the drive to proper “like-new” operating conditions. This includes making sure that any internal wearing parts with proprietary coatings function according to original specifications.
5. Choose OEM-certified service providers
Risk: Incorrect repair or maintenance work
Direct drives are complex, highly engineered systems. Third-party service shops that perform general industrial hydraulics repairs will typically not have the detailed equipment specifications or trained personnel to properly repair, calibrate and test the motor to like-new condition.
Reward: Job done right every time
Service facilities provide OEM-certified technicians fully trained in servicing direct drive systems, following detailed repair processes and specifications. Plus, by using service facilities, you automatically have original parts used in repair or maintenance work.
Best practice: comprehensive preventative maintenance programs
Work with your manufacture’s specialists to follow these best practices and implement a comprehensive preventative maintenance program. Specialists can visit your sites and perform detailed inspections of all accessible equipment and assess data points, such as motor temperatures, pump settings, speed and motor performance and other factors. They then provide detailed reports and recommendations on maintenance steps, parts replacements, and other follow-up actions.
Impact of “Breakdown Maintenance”
A major recycler had four Hägglunds hydraulic drive systems installed on critical equipment – and unfortunately, general maintenance practices were overlooked for years. When an unplanned drive shutdown occurred, Hägglunds service personnel went onsite and discovered issues on not just one, but all four machines:
- Hydraulic fluid was severely contaminated
- Pumps were completely worn out
- The Hägglunds motors significantly exceeded their service life
A major case of breakdown maintenance. The pumps and motor on the down machine were emergency shipped to the Hägglunds repair center for quick turnaround rebuild. The Hägglunds systems on the other three machines were sequentially taken out of service and sent out for repairs as soon as one set of equipment was returned, so at least some of the equipment could be kept in operation.
What preventative maintenance … prevents
The emergency freight, the quick turnaround repairs, and the downtime the recycler experienced incurred a tremendous cost – and could have been prevented. The recycler now has a Hägglunds Preventative Maintenance program that consists of two onsite visits per year. The annual cost of this program? About the same amount the recycler spent on emergency freight for just one Hägglunds drive. The payback? Peace of mind that going forward their Hägglunds systems will be expertly maintained – not just when breakdowns occur.
Bosch Rexroth Corp.
www.boschrexroth-us.com/hagglundsservice-recycling
Filed Under: Components Oil Coolers, Engineering Basics, Pumps & Motors, Trending