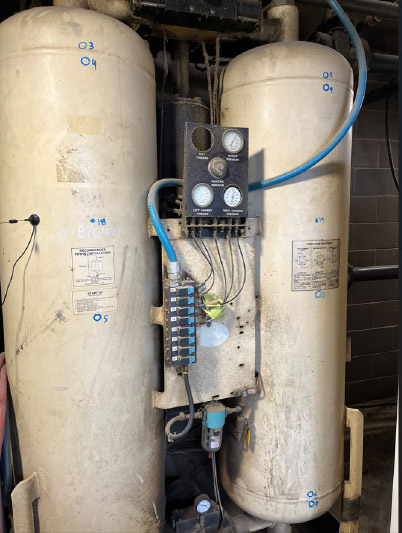
A wood products company had an aging heatless 1,000 cfm desiccant air dryer, being used to condition the compressed air produced by two 100-hp compressors in their processing facility. After working for many years, the dryer controller failed and had to be replaced. Replacement parts could not be found, so the local electricians came up with a solution using a PLC. Significant hours were spent on the project design, but finally the dryer was back in service.
A compressed air auditor was invited into the plant some time later to look at the compressed air system as part of an energy efficiency project. Instruments were placed to measure pressure, power, and flow — and it was determined the air dryer was consuming a major portion of the compressed air demand. At this facility, the actual process load averaged 140 cfm, yet the air dryer was consuming an additional 150 cfm of purge flow, representing more than 50% of the compressed air demand. The cost to feed this purge demand was calculated at $46,000 per year.
The compressed air auditor found that the actual required purge for a dewpoint-controlled dryer of this size should have been about 20 cfm average — not the 150 cfm that the uncontrolled dryer consumed. And he had another observation: none of the facility’s compressed air lines were exposed to freezing temperatures, so desiccant drying was not required in the facility. Replacement of this dryer with an efficient cycling style unit would reduce the operating cost to $580 per year!
The auditor explained that the dryer control conversion project was false economy. The repair was thought to save money on a new dryer — but in reality, significant costs were being incurred due to the decision. It was recommended that the dryer be replaced with the correct style and size for a large saving in operating cost.
Filed Under: Air Compressors, Air Preparation, Cylinders & Actuators, Pneumatic Tips