Sometimes, the smallest change makes the biggest impact. Here’s why one machine builder no longer adjusts proximity switches on pneumatic actuators.
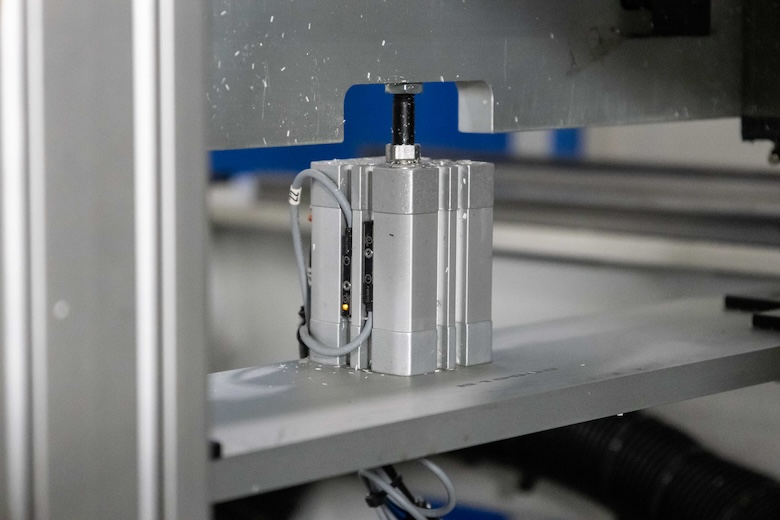
Proximity switches are used to monitor and control the position of pneumatic actuators. They include sensors that detect the presence or absence of an object within a specified range without making physical contact with the object. Depending on the type, they can detect changes in a magnetic field, capacitance, or inductance when the object comes close to the sensor.
Magnetic proximity switches are commonly used with pneumatic cylinders with magnets integrated into their pistons. They are usually mounted on the outside of the actuator and detect the magnet on the piston with each stroke. In many applications, these switches are used for end-of-stroke detection, ensuring the piston has reached its programmed position, either fully extended or fully retracted. An LED light on the switch often indicates when the end-of-stroke is achieved.
Since many proximity switches require a power supply to commission, original equipment manufacturers (OEMs) typically install and adjust them during a machine’s initial startup, then fine-tune them under full loading conditions. Though this process may only take a few minutes, machines can have several dozen switches in difficult-to-reach locations, compounding the time it takes to set up the machine.
Pro-Line Automation Systems, an OEM in Woodbridge, Ontario, installs numerous proximity switches in its automated CNC fabrication systems for window and door manufacturing. It previously used switches with a 2-mm detection range, which worked well for some applications but not all.
“We work mainly in the vinyl fenestration industry, and there’s a 2-mm range, especially for clamping material applications,” said Andrew Nauth, controls engineer at Pro-Line. “There is variance in material profile, even when it’s extruded. In situations like that, we have fluctuation, and sometimes that 2-mm range isn’t always consistent. When we expect a result and don’t get it, there’s an issue.”
A standard cylinder switch with a 2-mm detection range works well when the piston is hitting a hard stop on metal. However, with vinyl or polymers that have some give, a soft stop can prove challenging. Many of Pro-Line’s CNC systems cut vinyl, and signaling the piston end stroke often requires a detection range greater than 2 mm.
Previously, Pro-Line solved this problem by installing multiple sensors to mitigate fluctuation, which added wiring and programming requirements.
“It’s not always simple. It causes changes in programming documentation and down the line,” said Nauth.
With increasing demand for residential construction in North America, Pro-Line sought ways to expedite production, especially given labor and skill shortages. Nauth discovered Festo’s new SDBT-MSX proximity switch and learned it was a direct replacement for its machines.
“As a machine builder, we’re generally resistant to change because we have to support many machines and products, so we like to standardize. But we’re always seeing how we can improve our machines with the added benefits of new technology if it makes sense for us and our end users,” said Nauth.
What struck Nauth was the SDBT-MSX’s unique auto teach-in feature. Instead of locating each actuator in a machine and installing and commissioning each proximity switch at initial startup, Nauth and his team can set up and adjust the SDBT-MSX at a workbench before installation. When the machine is powered on and completes four cycles, the switch’s auto-teach capability automatically sets the correct final switching point without impacting the application.
“We used to mount the previous sensor on the cylinder, and then at power up, we’d have to adjust the sensor position to detect where the magnet is on the piston,” said Nauth. “The new sensor learns the position within a 15-mm range, and there’s no need to go back and adjust. When assembling the cylinders, we can mount the sensors on the end and not go back when we power on to find that specific position, which is a huge time saving for us.”
Pro-Line’s machines can have up to 50 pneumatic actuators with up to two proximity switches on each. Commissioning and adjusting switches the conventional way clearly eats up time, while the SDBT-MSX learns on its own.
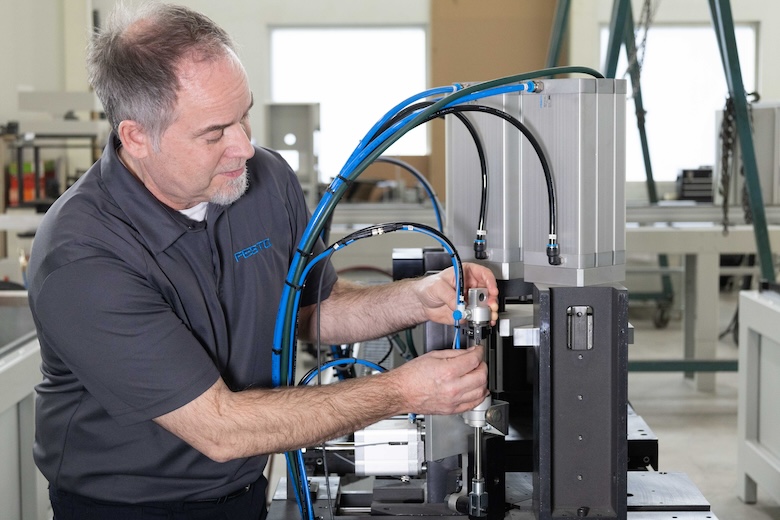
“The idea of the auto teach-in function is that the switch itself is looking for the magnet. Once the magnet comes into its initial detection range, it looks for it, and then it looks for it to repeat four consecutive times in the same position. Once it sees that, the switch can learn that position and store it,” said Darren O’Driscoll, product manager at Festo.
The aim is to make proximity switch installation quick and easy without needing to search for switching points and without a power supply.
“The adjustment feature that Andrew referred to is 15 mm, but when the switch is brand new out of the bag, the actual detection range is 20 mm,” said O’Driscoll. “A technician can put the switch in the two end positions, knowing that the magnet will be somewhere in that 20 mm, and then mount the cylinders, get everything connected, and connect all the cables. The first time the machine fires up is when the switch is connected to power, and that’s when it does its learning.”
The time-savings and simplicity even benefit end users who are replacing switches in their machines.
“End users have to go through the same process and may not be as well-versed as Andrew’s team. They may not know how to set up the switches properly and may do a lot of trial and error with a switch,” said O’Driscoll. “With the auto teach-in, if they follow the instructions, they can’t go wrong. So, it has a lot of benefits both for machine builders like Pro-Line and their customers.”
Pro-Line’s owner, Vinode Ramnauth, stated in a press release that the company’s sales have nearly doubled in the past five years. It’s expanding its U.S. market and anticipates doubling sales again in the next two years. The company is an eager early adopter of new technologies that make its staff more efficient and the biggest user of the SDBT-MSX in North America. And as it turns out, Pro-Line’s customers are already talking about the new proximity switches.
“One of our larger customers actually called me the other day and asked if we’re going to put these sensors — he called them ‘the smart sensors’ — on all our new machines coming to them. So, they’ve already seen a benefit on the end user side,” said Nauth.
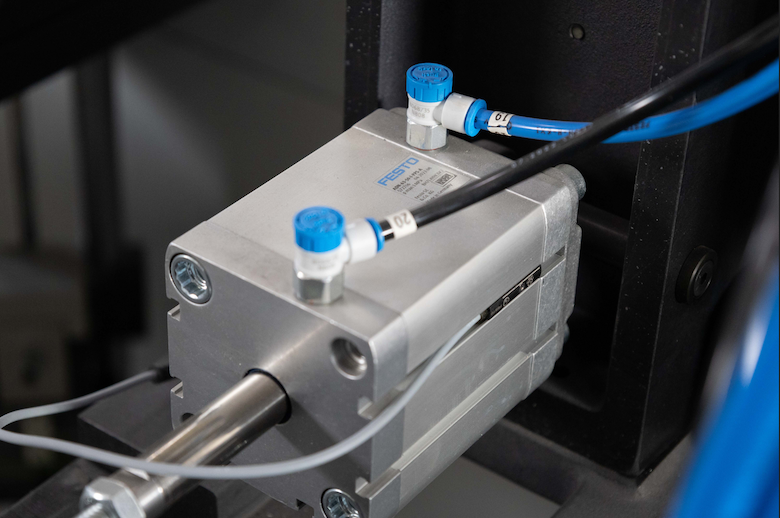
Any actuator with a T-slot mounting can use the new switch. It comes with default settings, but machine builders can change it from PNP to NPN and from normally open to normally closed. It can be used in its simplest form or programmed with as much functionality as needed.
“Anytime there’s a new technology, you have a hesitation,” said O’Driscoll. “I find that many machine builders are hesitant because it’s a new technology. They want to wait and see if there are any potential hiccups or problems and whatnot. We see Pro-Line as an influencer looking for new ways to be more efficient, make better products, and have better solutions for their customers. I’m hoping its story will influence other machine builders to make the same leap that Pro-Line did — all those sitting on the fence to take another look and go, ‘You know what, it’s time to give this a try.’”
Festo
festo.com
Filed Under: Components Oil Coolers, Cylinders & Actuators, Pneumatic Tips, Sensors, Technologies