Dale Dietel always knew there could be a better way to understand hydraulic system flows. Tired of the frustration born from the lack of easy flow monitoring, he invented his technology to provide continuous flow monitoring of all hydraulic functions — the world’s first Cartridge Flow Transmitter (CFT), from DGD Fluid Power.
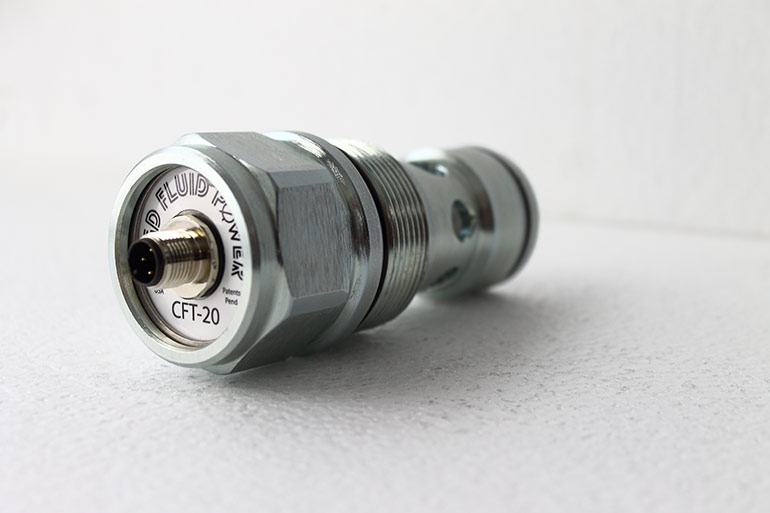
The CFT offers easy integration into hydraulic systems, requiring no additional hardware or connections for continuous flow monitoring of all critical hydraulic functions. It provides real-time data for predictive maintenance and remote troubleshooting and offers turbine flow accuracy. The CFT is available in standard M42 cartridge style design and Sun Hydraulics cavity T-18A.
The majority of hydraulic systems today use integrated circuits consisting of cartridge valves and associated devices. It is necessary to provide reliable and accurate data acquisition of all critical operating conditions inherent in hydraulic systems including pressures, temperatures, and flow rates. Currently, all existing devices to measure flow in a hydraulic system need to be installed external to any valve manifolds and are both cumbersome and expensive to implement.
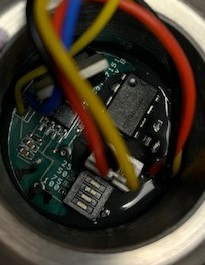
A patent is pending for the CFT, which is centered around the design of a turbine flow meter within a cartridge body. “The speed of the turbine is sensed differently than existing in-line meters on the market. Existing units use a sensor positioned to sense the tips of the turbine blades passing by. Currently, the geometry necessary to do this made packaging within a cartridge body impossible,” said Dietel. “To overcome this, my design uses a Hall Effect sensor to monitor the speed by sensing magnets in the hub of the turbine. This allows me to have the sensor placed along the axis as opposed to positioned on the circumference of the turbine. This also allows me to have a design without any dynamic seals or rotating parts other than the turbine, which rides on two bearing points on the shaft and with a finite spherical point against the sensing element.
“The internal parts of the CFT are manufactured from 316 SS to keep from disrupting the magnetic field. The turbine and support element are molded out of Delrin. The CFT is rated at a maximum hydraulic flow of 100 gpm but is designed with field adjustable electronics that can reduce the 4-20 mA outputs to work in the 12-gpm range. Standard switch settings are 25, 50, 75 and 100 gpm,” Dietel said.
What is unique about the CFT is the ability to design it into a hydraulic manifold. Current manifold assembly usually requires designers to disassemble in-line flow meters and reassemble the internal components inside integrated manifolds. The CFT eliminates the need to do that and makes replacement feasible as needed.
Industry response to the ease of use has been favorable. According to Thomas Wanke, Director of the Milwaukee School of Engineering’s Fluid Power Industrial Consortium and Industry Relations, there was nothing out there before that could do what the CFT can. “If you’re a person that’s troubleshooting and you’re looking at an industrial system that has integrated hydraulic manifolds with all these cartridge valves, this is the greatest thing since sliced bread,” Wanke said. “Because the problem with trying to troubleshoot any of those types of circuits, you have to break into them to make those measurements. Even in those integrated manifolds, you don’t have enough pressure tap locations just to measure pressure between different valves in the manifold block and now you can put in a cavity and permanently install a flow meter.”
Gary Gotting, President & CEO, Wandfluh of America Inc., added that the American-made design is portable, easy and fast to install. “This was designed by an experienced fluid power engineer that understands the needs of the industry intimately and designed it to meet an actual industry market need — not just because it was an engineer’s random thought,” Gotting said. “The well-built, robust design allows for wide flows to be measured.”
Gotting added that a standard M12 connector makes for easy interface with standard cables. He also said that the CFT’s wide operating range of 7-36 Vdc makes it compatible with both mobile and industrial applications, while its 4-20 mA output makes it much less susceptible to external electrical noise interference.
He said he sees the CFT being used in critical system circuits and systems — where failure would have significant impact. “It can be used as an integrated part of a manifold that will offer continuous and immediate operational information to allow preventative maintenance planning on key aspects of the system from pump output to filter condition to how the system is performing,” Gotting said. “And it can also be a standard installed part for remote equipment to report running health in real-time, i.e. wind power systems, oil recovery machinery, to prevent a catastrophic failure.
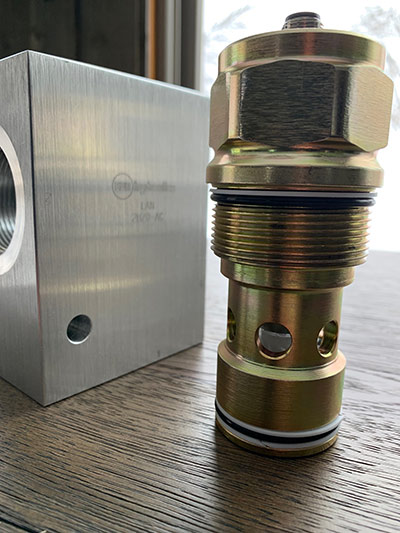
“(The CFT) is great for a field tech’s tool kit — a single cavity manifold and solid design offers easy hydraulic hook up into the circuit where needed,” he concluded. “Instant and continuous in-place measurement of the circuit performance gives users the ability to make earlier and faster decisions based on real data.”
The CFT can be used with hydraulic fluids, transmission fluids, oil-in-water emulsions, water and glycol mixtures and Skydrol. It has a recommended ISO cleanliness code of 17/15/12.
The carbon steel cartridge flow transmitter has a < 0.05 sec response time and ±0.5% full range accuracy. It is rated up to pressures of 5,000 psi and for temperatures between –20° to 70°C.
“I was motivated to design a cartridge flow meter to fill a perceived gap in the fluid power market for system diagnostics, predictive maintenance and troubleshooting. The industry has had pressure and temperature sensing devices for decades, but flow measurement had been limited to inline devices which are effective, but difficult to apply,” Dietel said of his design. “The design of the CFT also enables it to have minimal pressure drop; less than 1 psi/gallon.
“I am a fluid power professional and I realized that there was a gap in available diagnostic instrumentation used to monitor the performance of hydraulic systems and components. While there are many options to monitor and measure pressures and temperatures within a system, tracking fluid volume (flow) is limited to diagnostic equipment generally added to systems after a problem has occurred,” Dietel said. “This design is revolutionary and makes it easy to incorporate this device into a hydraulic system from both a design and a cost perspective. With the ever advancing and developing machine automation, Internet of Things (Iot) and Industry 4.0, closely monitoring fluid flow in a hydraulic system will enhance machine performance, lower operational costs, reduce downtime and enable improved predictive maintenance.”
DGD Fluid Power
www.dgdfluidpower.com
Filed Under: Mobile Hydraulic Tips, Sensors & Gauges, Trending