Learn some tips to ensure reliable, high-quality compressed air output at an affordable cost.
By Ron Marshall, Contributing Editor
It is crunch time. That important order needs to be processed by the end of the day. You are up against a deadline, and you only need a few more hours of production, and then the phone rings. The compressed air system is down and then everything stops. And when things start back up some ugly black gooey liquid starts seeping out of your compressed air pipes, ruining your final product packaging.
If you own or operate a compressed air system, you have likely been in a similar situation at some point in your career or have heard the horror stories of someone who has lived through this disaster. It’s almost as if the air compressors can smell fear, and respond by shutting down, and the pain you feel drives home how important the central compressed air system is to the operation of the whole plant.
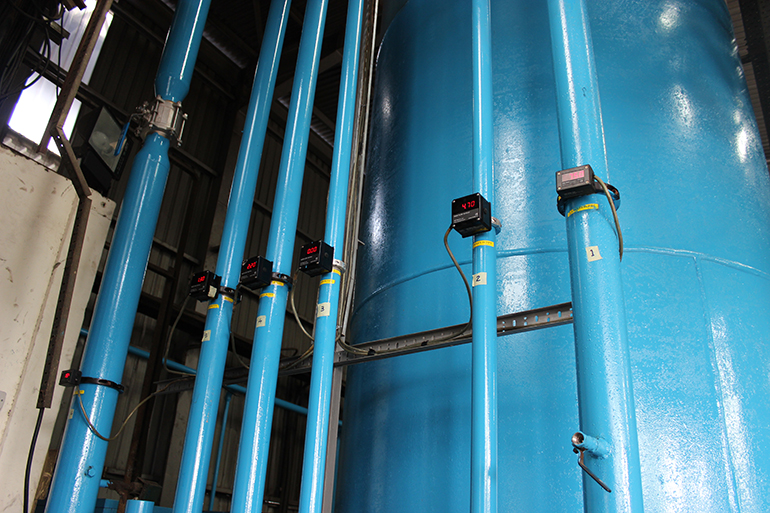
This article discusses the need for clean, dry and reliable compressed air and gives some tips on how to reliably achieve a high-quality output at an affordable cost.
Seeking the “Holy Grail” of air
There are many compressed air systems in the industrial world, and many thousands of uses for compressed air. An organization called The Compressed Air Challenge (compressedairchallenge.org) has created training to help compressed air system owners and operators understand their air systems and take steps to optimize their equipment.
In the first level of this training a very important statement is made relating to the needs for any compressed air system — A basic requirement statement for a good supply of compressed air is this, “A properly managed compressed air system results in clean dry stable air being delivered at the appropriate pressure in a cost-effective manner.”
This is an important but loaded statement containing six key elements:
- Manage — To adequately manage a compressed air system it must be measured.
- Clean – There needs to be adequate operating conditions for compressed air equipment and good equipment to filter and deliver clean high-quality compressed air.
- Dry – The dew point of the air must be lowered to well below the ambient temperature of the plant environment.
- Stable – To ensure stable pressure the compressed air system should be designed and fitted with reliable equipment with minimal pressure loss. A well-controlled system with adequate storage capacity will consistently maintain system pressure at a stable value.
- Cost-Effective – All of the above should be achieved efficiently with well running high quality equipment.
Managing by measuring
An often used, but appropriate statement is that you can’t manage what you don’t measure. Compressed air systems are notoriously bad in that regard. Sure, there are many pressure gauges all over to ensure people can see that the pressure levels are adequate, and if you are lucky some may be accurate. There will be a few temperature readouts on the air compressors, but most systems don’t have enough instrumentation to ensure your operators have a handle on the flow, power and energy consumed. And rarely are there any instruments to reliably measure air quality. This leads operators to operate blindly, and often leads them to make the wrong decisions on how to solve nagging problems.
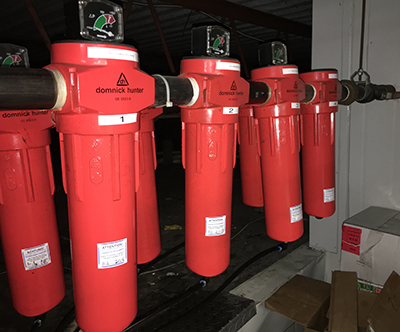
Over the years, the cost of high-quality instrumentation has come way down, so there is now no excuse for not having a full slate of instrumentation and a system of displaying the outputs so someone can easily assess when things go wrong.
Some basic equipment recommended to monitor your system:
- Pressure readings before and after air treatment equipment, and at critical locations in the plant
- Flow measurement at the output of the compressor room
- Power (kilowatt) and energy (kilowatt hour) metering on each compressor to enable the calculation and monitoring of key performance indicators
- Temperature monitors on the inlet of air-drying equipment
- Dew point monitors on the output of the compressor room
- Particle and lubrication detectors if you need to provide super clean air
- Handheld ultrasonic leakage detectors to find system waste
Ensuring a clean supply
Let’s face it, air compressors are like big vacuum cleaners — they suck in anything in their immediate area. If you have ever had the responsibility of keeping a compressor room clean you know it is a never-ending job — dust, debris, chemical vapors and hot humid air are drawn into the compressor to the detriment of the cleanliness of the produced compressed air. Filters on the inlet of the compressor stop the coarse dust (anything larger than about 5 microns), but smaller particles and contaminants in vapor form, even microbes, pass into the compressor and beyond.
When air is compressed and cooled, water condenses and mixes with the dirt, pollen, compressor lubricant, microbes and rusty pipe scale. This location before the air dryers is warm and oxygen rich — a great place for things to grow. This is why — if you have ever had the misfortune of spraying some condensate on your hand — it smells like an old gym sock.
Ensuring a clean supply of compressed air requires attention to these items:
- Ensure the rating of all system filtration is meeting with the quality requirements of your end uses.
- Filters pick up contamination, but don’t last forever so you must replace them regularly.
- In addition to properly rated main filters, sensitive equipment should have adequate filters installed at the end use.
- Don’t rely on the differential gauges installed on the top of filters because they often stick.
- Use high quality piping because standard steel pipe can shed particles well after main system filters have cleaned the air.
- Make sure your air-drying system is working well. How can you test this? Measure the dew point.
- If your system needs very high-quality air, install hydrocarbon detectors and particle counters.
Keeping the air dry
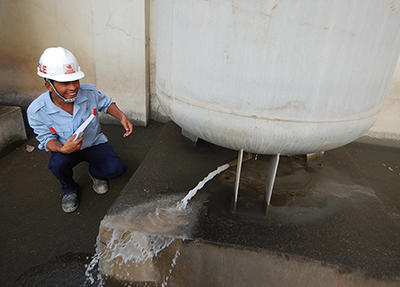
The flow produced by any air compressors is always 100% saturated with water when it comes out of the compressed air aftercooler. This air is usually above ambient temperature, so if allowed to cool, free water will drop out and be carried along with the flow of air in the system piping. This can contaminate downstream equipment and products. To produce dry air, some method of air drying needs to be installed.
The most common drying method is a refrigerated dryer type that cools the flow of air within the dryer, separates out the condensed moisture, then reheats the air to near ambient. The result is a flow of air with a dew point of around 35° F. This is adequate as long as the plant’s piping does not fall below that temperature, however, some sensitive products require dewpoints of below –40°. This requires desiccant dryers using internal moisture adsorbing beads. It should be noted the cost of producing very dry compressed air at this quality is at least five times more.
The biggest common problem with air drying equipment is overheating. As the temperature of the compressed air increases, every 20° doubles the amount of water vapor. This becomes a problem, for example, on the hottest and most humid summer days. If your compressors are air cooled, and the ventilation in the compressor room is lacking, air dryers can easily see excess temperatures on their inlet. Unfortunately, most dryers are only rated for about 100° inlet conditions. If the temperature exceeds this in any way there will be trouble.
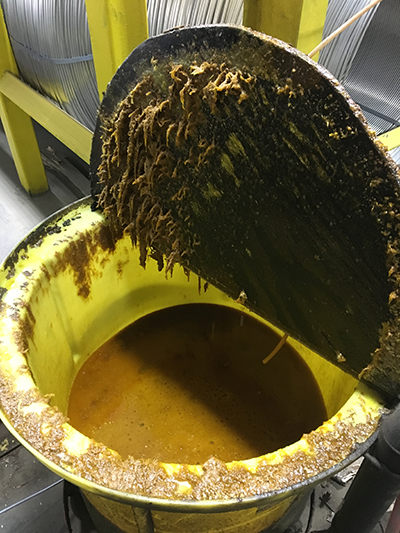
Some tips about air dryers and moisture:
- Plan for dryer failure, slope pipes properly for drainage, take air off the top of the pipe, and install drains on low spots.
- Ensure the inlet air to dryers is as clean and as cool as possible, as heat is almost always the cause of moisture in the air.
- Know the dryer ratings. If they are exceeded in any way you should oversize for worst case conditions.
- Maintain dryers, especially condensate drains within dryers and filters, to ensure they always work. Failed drains are the second most common cause of water in the compressed air.
- Choose dryers for low pressure differential to save energy.
- Choose cycling or dew point controlled dryers to save energy.
- Realize the display of refrigerated dryers does not measure dew point; rather, it is an indication of the temperature within the dryer. A failed drain or heat exchanger in the dryer can still allow moisture to pass through.
- Measure dew point with an accurate instrument to ensure you are warned when things go wrong.
Producing a stable pressure
Achieving stable plant pressure is all about reliable and accurate compressor control and the minimization of pressure drops in components.
Control of system pressure means you must put exactly the amount of air you are using into the system as you are taking out. If you do this, you reach equilibrium, and the pressure is constant. And you must have a significant amount of air stored in a large air receiver to ensure you can ride out large system events with only a small fluctuation in pressure as the system adjusts.
The system must be designed and sized so that any peak requirement can be covered by adequate compressor capacity, and consider any future increase, such as what might happen if a significant level of leakage develops. Making sure this selected equipment is properly sized and operates in a well-controlled manner is important. These days the best pressure control is achieved if one or more compressors in a system is a properly sized variable speed-controlled unit.

When a system has more than three compressors it usually becomes economical to install some sort of sequencing controller to orchestrate the operation of compressors to ensure precise air pressure.
Tips for stable pressure:
- Ensure compressor controls are coordinated to ensure optimum pressure delivery.
- Make sure system storage is at least 5 gallons per cfm times the capacity of the largest trim compressor.
- Choose system components like filters, piping, dryers with the lowest possible pressure drop.
Operating in a cost-effective manner
Ensuring the system operates in a cost-effective manner requires two things: first, you must produce the air in the most efficient manner possible, and second, you should produce as little air as possible. To achieve these points, the selected equipment must be run in the most efficient manner, with the least pressure drop, and the lowest possible pressure. And compressed air waste needs to be managed though the reduction of leakage, artificial demand (flow caused by high pressure), and inappropriate uses of compressed air. To achieve these goals you need assistance. As a start, learn about these various efficiency measures in Compressed Air Challenge’s Fundamentals of Compressed Air Systems seminar. And then call in some experts to help you out.
Conclusion
By measuring your system, and taking some care in how things are purchased, sized, operated and maintained, you can come very close to perfection. This can help you achieve a properly managed compressed air system supplying clean dry stable air being delivered at the appropriate pressure in a cost-effective manner.
Ron Marshall is the owner of Marshall Compressed Air Consulting. He has 26 years of experience in the compressed air optimization field and provides training, technical writing and compressed air audits to his many clients.
Filed Under: Air Preparation & Regulation, Compressed Air Technologies, Engineering Basics, Pneumatic Tips