By Justin Fluegel, Contributor
A simple example of explaining a self-relieving pressure regulator is to imagine having a balloon with two normally closed ends. Call the ends supply and exhaust. Assume the balloon is empty and you ask for more pressure in the balloon. The supply end opens until the balloon pressure equals the requested pressure, then the supply end closes. If the balloon’s pressure exceeds the requested pressure or you ask for a lower pressure, the exhaust end opens until the requested pressure is reached, then it closes. A self-relieving regulator maintains the requested pressure in the balloon with supply and exhaust.
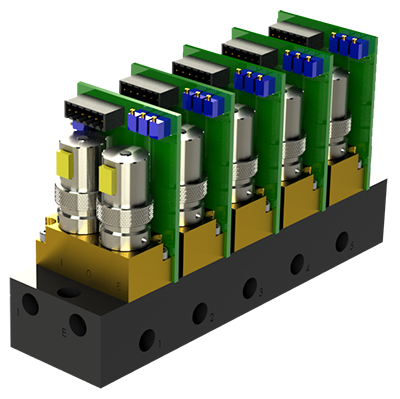
Electropneumatic pressure regulators combine the pressure regulator with an electrically controlled proportional solenoid. These valves require either a controller of their own or the control signal is integrated into a Programmable Logic Controller (PLC). What makes these valves unique is the pressure can be adjusted electronically in real time based on feedback from the machine.
The electrical solenoid can be actuated by either voltage or amperage from the controller/PLC. Typically, a voltage drive solenoid uses 0 – 10 voltage direct current (VDC); while an amperage driven solenoid uses a current of 4 to 20 mA. These electrical values are programmed in proportion to the pressure range of the pressure regulator. As an example, a 1 V (10%) change in the voltage to a solenoid would change the pressure by 10% or 12 psi in a 120 psi application.
Control of a proportional regulator can be done utilizing a simple Direct Current (dc) potentiometer for manual adjustment. Process controllers are available from a variety of manufacturers and can be used to monitor the input signal and control output using proportional integral derivate (PID) to maintain system stability. PID uses the feedback loop from the controlling system to refine the output of the controller. P (proportional) accounts for the error rate in the system. I (integral) accounts for past values of controller. D (derivate) is the best estimate of a future trend.
Some valve manufacturers offer their own controllers to pair with the proportional pressure valves. Options exist on the market for proportional pressure regulators with integrated pressure transducers, offering a faster reaction time for the valve. Typically, the proportional valve can adjust in time measured in milliseconds. If part of a larger machine or system being controlled by a PLC, it can be used to receive, analyze, and process the feedback signal. The PLC will then send the signal voltage or amperage to the solenoid.
Filed Under: Air Preparation & Regulation, Engineering Basics, Pneumatic Tips