Pressure regulators, as the name indicates, control the pressure in a pneumatic circuit. Setting and maintaining pressure in a system is important for safety and energy efficiency of individual actuators, tools and instruments as well as for the complete circuit.
A typical manufacturing facility has plant air pressure from the compressor set to around 110 to 120 psi, which will gradually decrease, depending on friction and restrictions in pipe and fittings and pressure drops through dryers, filters and other devices. When a specific process or application requires compressed air pressure to be maintained within certain limits, pressure regulators are a must.
Users should select a regulator based on an analysis of system characteristics, including input pressure, required outlet pressure, approximate flow, pipe size, and degree of precision required. Other considerations might include response time, sensitivity and repeatability.
In past decades, basic manual pneumatic pressure regulators consisted of a valve that included an internal pressure-sensing element, and some means to provide a reference force. In many regulators, a diaphragm or piston sensed the air pressure, and a regulating spring provided the reference force. In essence, the diaphragm acted as a force-balancing system. An imbalance between the reference force and force generated by the outlet pressure moved the diaphragm, which actuated the valve and, in turn, restored the balance.
Up until about the turn of the century, various electropneumatic versions built on this fundamental mechanical technology. As the name indicates, they converted electrical current or voltage signals into pressure. They worked by creating a force imbalance on a piloted diaphragm by such means as a magnetic voice coil. No other electronics were used to control the pressure output. Like the purely mechanical version, the device relied on a simple force balance with adjustable spring biases for the zero and span. The regulators often contained a second flow-boosting stage to generate higher flow rates at the outlet port.
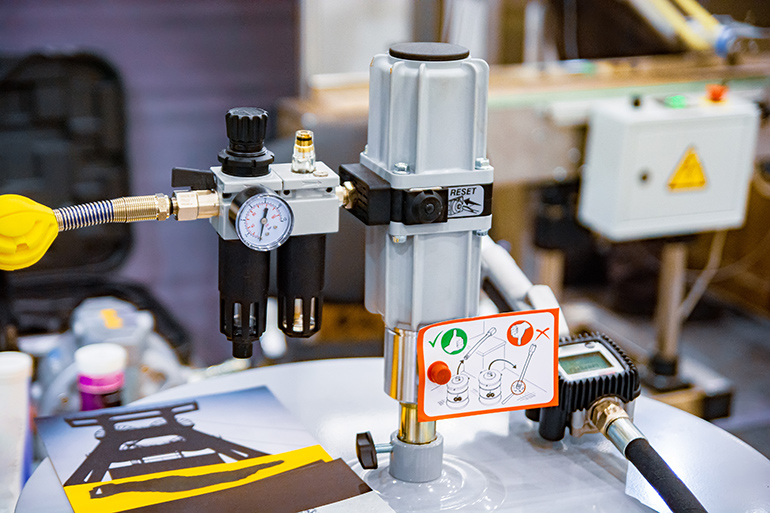
While technicians had to be trained to adjust the zero and span screws to ensure the required accuracy and repeatability, the devices offered good performance if properly maintained and frequently calibrated. These types of products are still used today, although most users have migrated to regulators that rely on internal electronic feedback, which offer higher accuracy and performance.
These products typically house valves, internal pressure sensors and electronic controls. Such electronic pressure controllers often use high-speed servo or solenoid valves, or direct-acting voice-coil units, to increase or decrease gas pressure as needed. They offer high precision, high repeatability, and low hysteresis, along with robust construction and good reliability.
Pressure is generally controlled by two valves. One valve functions as the inlet control, the other as the exhaust. In operation, internal pressure sensors track conditions and send signals to the electronic controller, which uses PID or similar algorithms to interpret the data. This feedback signal is compared against the command signal input. A difference between the two signals causes the controller to send a correction signal to open one of the valves and allow flow in or out of the system. Thus, the electropneumatic regulator maintains accurate pressure by controlling these two valves, with output pressure proportional to an electrical signal input.
Models with analog or digital electronics can be compatible with serial communication networks such as RS-232, Profibus or Ethernet/IP.
Some electropneumatic regulators offer two-loop control, which takes advantage of an external feedback signal. This setup is preferred when pressure must be maintained at a distance from the regulator. In this case, an external pressure transmitter is connected to the process, and its signal serves as the primary feedback signal that the controller compares against the command signal input. This, in turn, commands the internal control loop to initiate valve actions.
This makes it possible to control parameters other than pressure. For instance, a linear-displacement transducer can send electrical feedback signals to the regulator, and the controller will adjust output pressure to match the set-point signal and control air cylinder motion. Other types of sensors let users control parameter such as force, torque or flow.
Filed Under: Air Preparation & Regulation, Pneumatic Tips