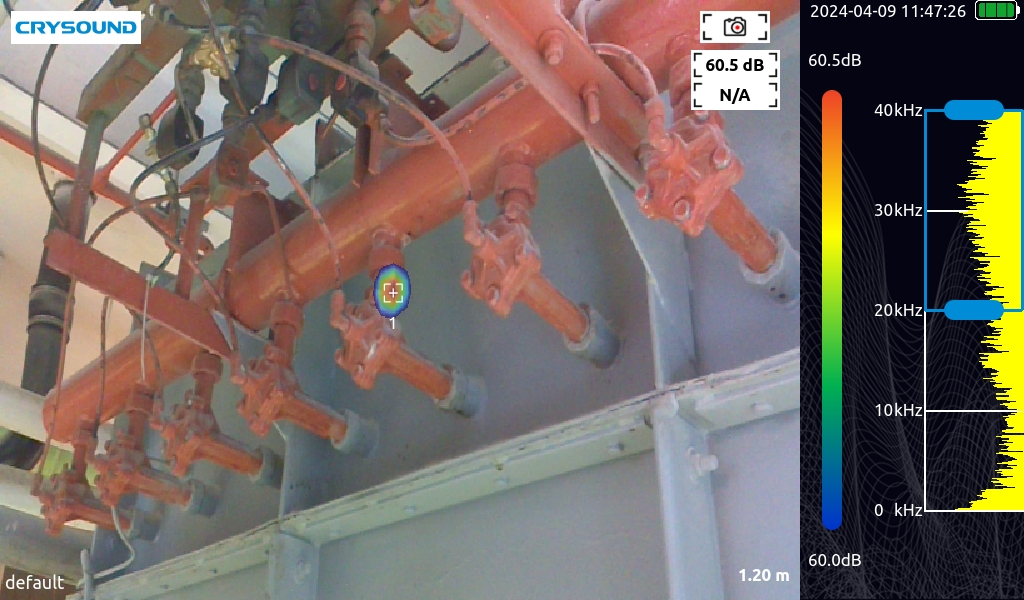
Dust collector reverse pulse cleaning is commonly deployed in any industry that creates powdered dust. Through the years, it is common to see expensive failures of these devices that consume excessive amounts of compressed air. Often times, these failures go undetected.
Dust collector reverse pulse cleaning is a highly efficient method for removing accumulated dust from the filter media within dust collection systems, commonly used in industrial environments to maintain air quality and protect machinery. This cleaning process employs short, high-pressure bursts of compressed air directed backward through the filter to dislodge dust. The pulse is injected through the filter in the opposite direction of the normal air flow, typically through a venturi nozzle, which enhances the cleaning effect by rapidly expanding the air as it passes through. This sudden expansion causes a shock wave over the filter’s fabric, shaking loose the dust cake without damaging the filter material.
The process is typically automated and controlled by a timer or a differential pressure sensor that measures the pressure drop across the filter. When the pressure drop indicates that the filter is becoming clogged with dust, the cleaning cycle is initiated.
Some commonly found compressed air problems with dust collectors:
- Lack of storage capacity reduces the power of the pulse, causing operators to increase pulse duration and frequency, causing early failure of the filter medium.
- Failed valves, either not firing, allowing the filter to clog up or failed open consuming large volumes of compressed air that pulls down plant pressure, often going undetected for months on large systems.
- Differential pressure controls turned off wasting compressed air.
- Minor leaks in supply components such as fittings and tubing.
- Major leaks due to manifold failures and valve diaphragm failures.
- Dust collectors, causing fluctuations in system pressure, affecting critical pressure operations.
If dust collectors with compressed air cleaning exist in your plant, it is wise to carefully maintain and monitor these to ensure efficient and effective operation. Constantly check for leaks and abnormal operation — and repair as required.
Filed Under: Air Compressors, Air Preparation, Components Oil Coolers, Compressed Air Technologies, Pneumatic Tips