When doing a compressed air audit, it is always recommended to measure the important parameters of the system and analyze the data carefully. Typically, pressure and power (or amps) are monitored, but in some cases measurement of flow comes in handy. In the case of a large plumbing component manufacturer, the installation of flow meters detected a surprising problem with two of their compressors.
The system was made up of six large compressors distributed in three different locations within the plant. The compressor operation was very efficiently coordinated by a central compressor controller. The controller also did some reporting of compressor peak and average flows for the information of the operators.
The system originally had no flow meters installed, but staff were interested in how well the compressors were producing, so flow meters were installed to monitor the output of all the units. When this was completed, data loggers were installed to capture the data for analysis in assessing system operation. This provided quite the surprise! It was discovered that two of their compressors were only producing about half of their rated capacity.
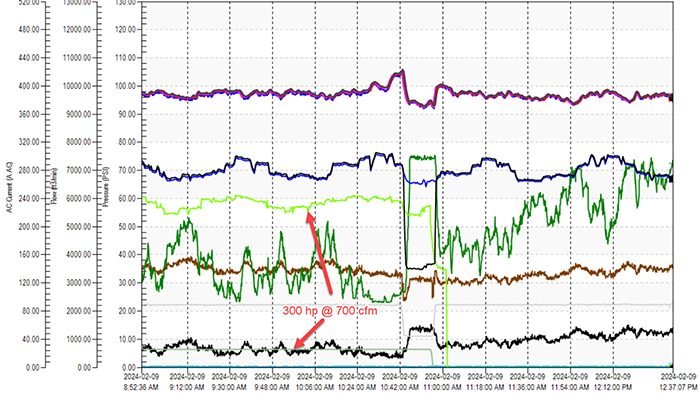
Investigation was performed and it was found that these two compressors had variable displacement controls (called turn valves). These controls were designed to cut back the capacity of the compressors — if they were needed to run in part load. However, this type of control was not needed for this particular installation. The controls had been incorrectly adjusted to cut back the compressor capacity, but nobody noticed, due to the lack of flow measurement. The installed central compressor controller incorrectly assumed that when each of the compressors was loaded, it was producing full flow — causing operators to believe that all was well.
After a few quick adjustments by their service provider, the compressors were set back to full load output. The new flow measurement and resulting adjustments had uncovered about 1,000 cfm of extra system capacity and increased the system efficiency.
Filed Under: Components Oil Coolers, Compressed Air Technologies, Pneumatic Tips