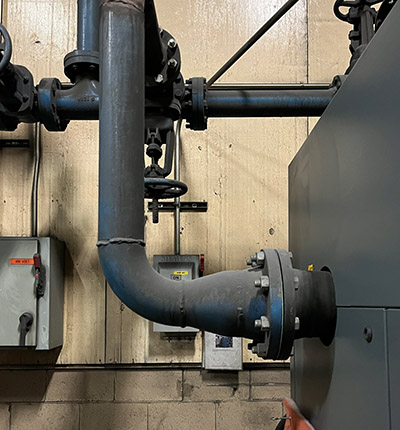
A compressed air auditor was assessing a compressor and dryer installation within a compressor room and noticed something strange. On a large air dryer, the outlet flange was of 6-in. size, yet the piping used to connect the compressors and filters to the air dryer was only 4-in. Further to this, the long piping link connecting to the main plant distribution was also 4-in. A piping size transition was installed to connect the small piping to the large flange on the dryer as shown in Fig. 1.
Using measurement instruments, the auditor measured the pressure drop between the compressor discharge and the outlet to the system and found a possible problem. During low loads — when only one compressor was running — the pressure loss was minimal. However, when all the compressors within the compressor room ran at peak capacity, the pressure differential was more than 10 psi, which is excessive for an industrial compressed air system.
Pressure loss in a compressed air system, caused by friction, varies exponentially with square of the flow change. So even a small change in flow can cause a large change in pressure differential. Doubling the flow across a 3-psi piping restriction will cause a the pressure differential to rise to 9 psi. In this case, the pressure loss was as high as 12 psi at peak flows, causing the compressor discharge pressures to be set higher than normal to overcome this loss. The higher the compressor discharge psi, the more power they consume. The relationship is about 1% more power for each 2 psi in higher pressure.
Flow meters were installed on this system so the flow velocity could be checked. It was found that the flow velocity during peak production was about 50 feet per second, much higher than desired. This was causing significant pressure loss. Typical pipeline velocity in a well-designed system maintains peak flows of between 20 to 30 feet per second within the compressor room. A good way to calculate pipeline velocity is to use USDOE’s Measure Tool.
There is often a good reason why air compressor and dryer outlet flanges are sized the way they are, but be aware not to reduce piping size to cause excessive restrictions.
Filed Under: Components Oil Coolers, Compressed Air Technologies, Pneumatic Tips, Technologies