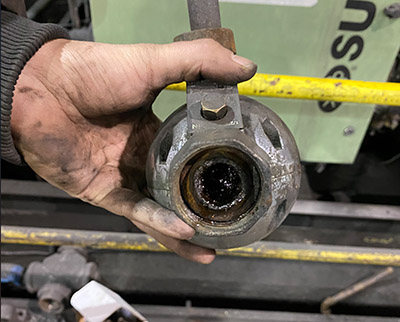
A compressed air auditor had a system of measuring devices that was monitoring a compressed air system located in a metal foundry. Pressure, flow, and compressor power were all monitored to help determine if the system was running efficiently and effectively. An additional set of instruments were added to the monitoring suite due to some reported water contamination problems within the plant; these sensors measured compressed air dewpoint and ambient temperature.
When compressed air is produced, water is squeezed out of the air and must be removed or downstream contamination will occur. In addition to this, the discharge air from the compressors is 100% saturated, so even one degree of cooling within the pipes will condense water and compressor lubricant into the air stream. For this reason, water separators and filters need to be used to remove liquid contamination. Condensate drains are fitted on these devices to efficiently remove the liquid from the system — while keeping the compressed air.
A short time after the extra monitors were installed, it became obvious something was wrong at the plant’s West compressor station. The dewpoint produced by the site’s refrigerated air dryer was climbing above ambient temperatures, at which point water formed within the piping. A quick test of all the system drains did not show any obvious problems. When the test ports of the drains were operated no water was released, a sign that the drain was removing the collected water from the filters, but even still the problem persisted.
The maintenance staff investigated further and found the drains on the system’s main filters were completely full of contamination (Fig. 1). This black ugly mess, with the consistency of grease, had totally plugged up the drains, preventing them from releasing any liquid whatsoever, even when the test port was opened. Maintenance was done on the drains to bring them back to normal operation — and the dewpoint returned to normal.
This proved another example of the value of system monitoring and the power of full investigation when problems are detected!
Filed Under: Components Oil Coolers, Compressed Air Technologies, Pneumatic Tips, Technologies