A compressed air auditor visited a large mine and was asked to look for areas of improvement. The mine’s manager was interested in reducing the electrical consumption and had a hunch that the compressed air system was a good item to investigate.
The facility was a very mature site, so there were many large compressors feeding miles of compressed air lines extending more than 6,000 feet deep. The complex seemed like a large three-dimensional puzzle that needed to be explored. When the auditor checked the flow patterns to the mine, he found that even during non-production activities, the compressed air system consumed more than 10,000 cubic feet per minute of compressed air flow! This was costing almost $2 million dollars per year in electricity.
Looking for leaks is challenging in a typical large industrial compressed air system, but this site was complicated. There were so many air lines withing the dark, damp passages — and on so many different levels. To solve the problem, the auditor proposed using a new type of leak detector called an acoustical imager.
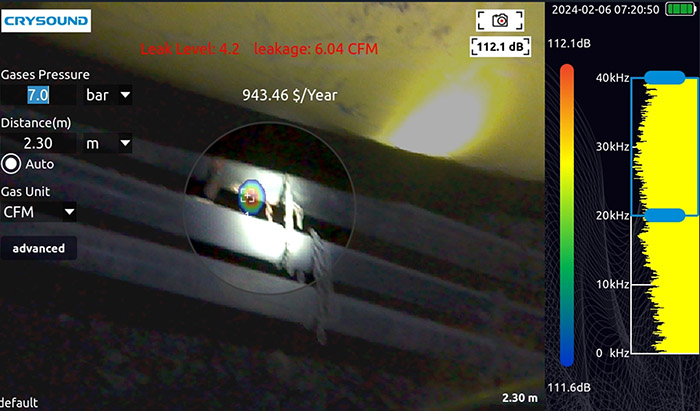
An acoustical imager locates compressed air leaks by detecting the ultrasonic sounds that are produced when air escapes from high to low-pressure areas. Equipped with a sensitive microphone, the imager identifies these frequencies — even in noisy industrial environments — and processes the signals into audible and/or visual forms for the operator.
The directional capability of the device helps pinpoint the precise location of the leaks, showing them on a screen overlaid with an image of the viewed piping or equipment. Some imagers can also estimate the size and rate of the air loss, enabling prioritization and efficiency in maintenance efforts.
The auditor had the maintenance staff drive through various areas of the mine while operating an acoustical imager from the back of the maintenance buggy. In this way, the various passages could be quickly explored, and significant leaks could be identified, even in the dark. The auditor called this method “drive by shooting.”
Not surprisingly, quite a number of significant leakage locations were quickly located — and when fixed, will provide a quick saving in waste-related energy costs.
Filed Under: Components Oil Coolers, Compressed Air Technologies, Pneumatic Tips