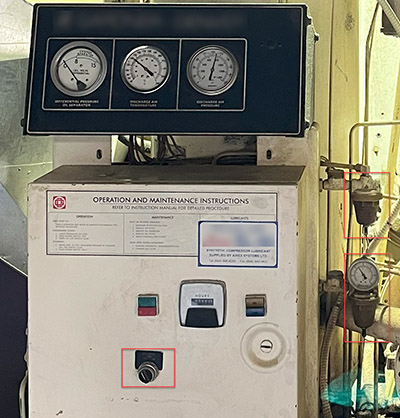
Recently, a compressed air auditor ran across a newly rebuilt compressor at a wood products company. The unit was cleaned up nicely and had a shiny new air end due to a rebuild — but because the unit had obsolete controls, this compressor continued to run very inefficiently. Saving money by rebuilding this compressor was false economy.
Paraphrasing a crusty old air auditor, since passed on, “You can shine it up all you want with a nice coat of varnish, but in the end all you are left with is crap.”
The compressor in question was sent for repair because it couldn’t hold pressure. Lack of capacity was the suspected issue, so air end failure was suspected. However, when the unit returned, after the expensive repair, the pressure problems continued. Closer inspection by the air auditor found the unit had both modulation and variable displacement controls, both adjusted by turning a bolt on the bottom of the subtractive pilots placed on the right side of the units (red boxes).
These controls were not coordinated properly, resulting in the air end being permanently set to half capacity and below. This caused low pressure when the compressed air demand exceeded the available capacity, which was less than half the rated capacity. Very often, units such as these are incorrectly adjusted because many well-meaning but poorly trained technicians have wrenches.
Newer, more modern controls, have electronically adjusted settings. The newer compressors are also much more efficient than the old units — manufacturers have made great advances in compressor technology.
Lesson: When repairing a failed compressor, owners and operators should consider that a rebuild may not be in their best interest if they want to save operating costs in the long run.
Filed Under: Components Oil Coolers, Compressed Air Technologies, Pneumatic Tips, Technologies