Moog Inc. has delivered a high-performance test system for Spain-based Piedrafita Systems that the company now uses to design vehicle suspensions. Among its current projects, Piedrafita is using the new test rig — installed in July 2023 — for the SRB Project, which aims to develop a revolutionary hydropneumatic rotary suspension for armored vehicles. Through a grant from the EDIDP (European Defence Industrial Development Programme), Piedrafita launched the SRB project.
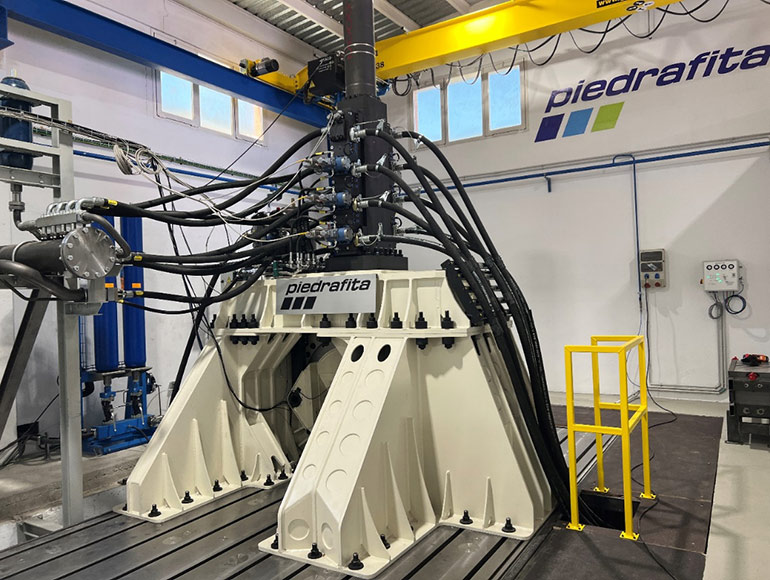
Test System for 70-ton tracked vehicles used advanced hydraulics and controls from Moog Inc. (Source: Piedrafita).
The catalyst for the new test system was Piedrafita’s need for technology that could deliver forces up to 500 kN at a speed of 8 m/sec, and up to 200 Hz. Piedrafita called Moog, with whom it had collaborated in 2012 to design a fatigue test bench for developing a shock absorber. The fatigue test bench Moog designed in 2012 delivered up to 80 kN at 4.4 m/sec velocity.
“Piedrafita asked if this new system was feasible,” said Juan Carlos Molinero, project manager and engineering leader for Simulation & Test at Moog. “After our study and performance tests, we again collaborated with Piedrafita to develop a concept that could test an armored vehicle’s suspension.”
“Working with Piedrafita, our engineers designed the new test bench with a high-performance controller and customized actuators reproducing vibration up to 100 g,” noted Ian Whiting, chief engineer for Moog. “It’s an example of how we innovate with our customers to design and manufacture the most advanced motion control systems for incredibly demanding applications.”
The newly developed test bench simulates the passage of an armored vehicle’s tracks over undulating terrain. This level of vibration is essential for evaluating the resistance and performance of shock absorbers as well as suspension systems in combat.
“Our new test system is capable of carrying out tests for 70-ton tracked vehicles, with a weight of around 5.5 tons per wheel,” said Vanesa Recio, head of Communication and Marketing for Piedrafita. “Our engineers can test wheel stations under very demanding profiles for main battle tanks such as the Abrams, Challenger, Leclerc, and Leopard.”
The test system includes a Moog Test Controller, two hydraulic actuators with Moog Digital Servo Valves, an HPU with Moog Digital Pumps and a power cabinet, and an accumulator bench with the required piping. As part of the design and installation, Piedrafita asked Moog to select and size the new test system’s respective components. Along with its commissioning, Moog trained Piedrafita to operate the system.
Molinero added that all system parts (e.g., HPU, accumulators, hydraulic service manifolds, seismic mass, frames, actuators, controllers, etc.) are designed to work with and withstand very high energy and vibration levels. Several megawatts of dynamic power need to be continuously managed during testing. Two axes act upon the test specimen, each operating in its own (isolated) frequency range. Combined, they provide force, velocity, and acceleration levels over a frequency range, which are impossible to meet with a single axis (actuator).
He expanded on the actuator specifications as well. “We have used hydrodynamic actuators without pressurized seals and permanent internal drains. The nominal pressure is 280 bar. The peak flow could reach over 8000 lpm,” Molinero said. “The high-speed actuator can accommodate up to eight three-stage, high-flow Moog servo valves with digital pilot (valves).”
Molinero said that several 210 lpm Moog digital pumps were installed to allow for easy control of the system flow and pressure (5 to 280 bar). “Furthermore, we have digital connections for all the pumps to balance the energy contribution (of each pump) and let us monitor the system consumption as it happens,” he said. “The system can operate at a wide pressure range, also at low values to properly manage the energy and the safety conditions.”
“The high-performance test bench minimizes costs and enables tests in a controlled manner rather than driving over a proving ground, thereby protecting a crew who would otherwise have to be on board a vehicle,” Recio added. “Manufacturers such as General Dynamics and KNDS can also test their vehicles’ suspension on our new test system.”
Moog Inc.
www.moog.com
Piedrafita Systems
piedrafita.com
Filed Under: Components Oil Coolers, Cylinders & Actuators, Technologies, Valves & Manifolds