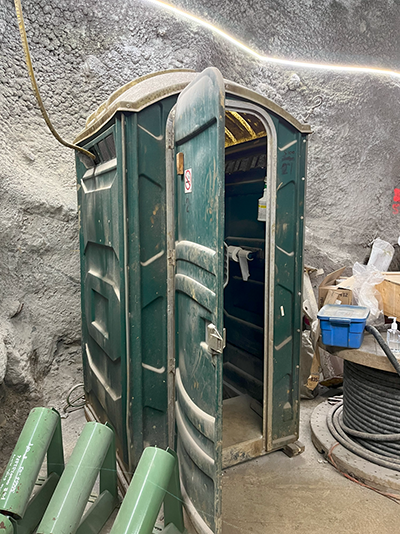
Compressed air is useful for very many important tasks in facilities. However, due to the high cost of producing it, there are some end uses that are very wasteful. Air conditioning and ventilation is one such inappropriate end use.
In a recent survey, a compressed air auditor found a surprisingly unique waste of compressed air in a mine. Underground conditions are quite hot and humid, which causes worker discomfort, so the go-to cooling and ventilation method is using 100 psi compressed air. The figure shows the application of compressed air to a portable toilet. This cooling method is low tech. Just simply a cracked open valve sending compressed air to a hose positioned within the booth to cool the worker. Estimated flow to the toilet is 20 cfm consuming 5 kW of equivalent power, but this application has complications.
As load grew in this complex, the compressed air system got larger and larger. More and more compressors were added over the years — until the electrical limit was reached. To supply the power to some new compressors, a generator needed to be added that consumed natural gas. Use of fuel generators to produce electricity is much less efficient than providing power from the utility grid. When asked to calculate the costs, the facility personnel were very surprised.
When all the costs were added up, the final tally concluded that the power feeding the new compressors was costing about 35 cents per kWh — rather than the 6 cents for the utility supplies electricity. That’s almost 6 times the cost. Therefore, the air-conditioned toilet in this case was costing about $15,000 per year to operate, even though it is occupied only a small fraction of the time, or so management hopes.
Further investigation revealed many other similar uses of compressed air from ventilation of toolboxes to cooling large service bays with compressed air powered air nozzles. After a good head shake, an investigation of possible solutions is underway.
Filed Under: Components Oil Coolers, Compressed Air Technologies, Pneumatic Tips, Technologies