When the equipment is new and set up correctly, the coordination of VSD air compressors with fixed speed units is quite easy — if the number of compressors in the mix is four or less. Typically, what should happen is the VSD compressor maintains trim position with all combinations of fixed speed compressors providing base load duty, provided the sizing of compressors has been chosen correctly.
To avoid an undesirable condition called control gap, the variable range size of the VSD range must be equal to or larger than the biggest fixed speed compressor with which the VSD must work. If this is the case and the remaining compressors are set up like shown in Fig. 1, the VSD will always maintain trim position (taking partial loads) and everything will work correctly.
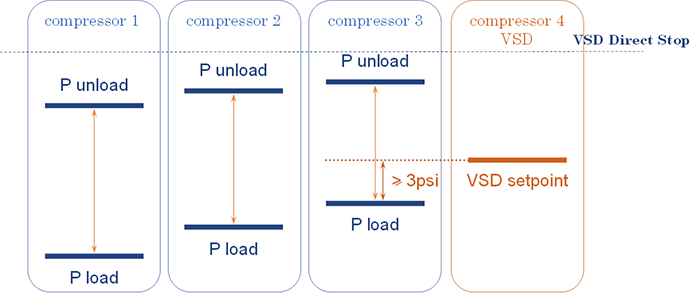
But as time passes, things often go sideways with compressor coordination. This is true of a compressed air system at a plastics manufacturing plant. Rather than using the precise and accurate pressure regulating capability of VSD control to maintain a pressure, the offending system was corrupted by some well-meaning but misinformed service technician. The pressure settings were altered so that the VSD was no longer trimming, it was loading and unloading in second position, while running at full speed on loading cycles.
This resulted in the compressed air system becoming less efficient because of significant unloaded power consumption. Also, the pressure profile exhibited a varying sawtooth waveform, with two levels of setpoints, resulting in widely varying system pressures, depending on which compressors were running. A correctly set up system would have a constant flat pressure profile controlled by the VSD setpoint, with fluctuations downward and upward only when an additional compressor needed to be loaded or unloaded.
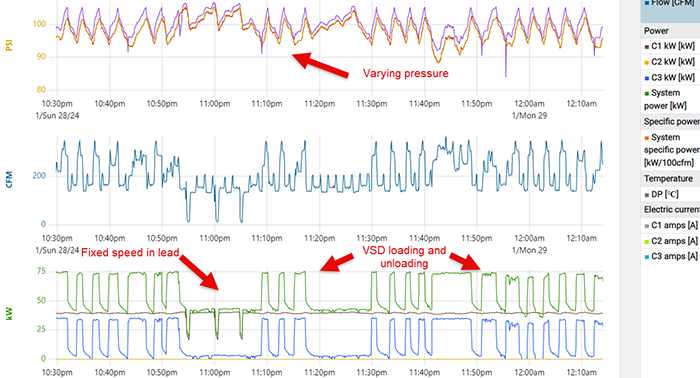
The recommended solution for this system is to return the setpoints to the originally intended values, which is an easy fix by pushing a few buttons. The plant plans to document the proper operation and do training so this problem does not happen again.
Filed Under: Components Oil Coolers, Compressed Air Technologies, Pneumatic Tips, Technologies