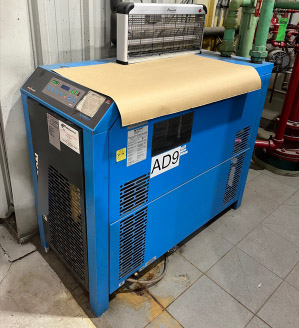
A compressed air audit at a metal parts painting plant yielded some puzzling results. Pressure loggers were placed at the compressor discharge and in the plant, but the readings were showing an unexpected and significant pressure drop between the instruments. Visual checks showed that the only thing between the loggers was an air dryer with no inlet and outlet filters and a length of well sized piping. Checks on the dryer refrigeration system showed everything was normal, the dryer was not frozen.
Closer inspection, however, found that the type of refrigerated air dryer used had a special design. To gain highly efficient water separation from the dryer airstream, a coalescing dryer was used, rather than a centrifugal separator. In the years since the dryer was installed, the filter element was never replaced — and it had developed a large pressure differential. This pressure drop robbed the plant of adequate pressure and caused the compressor pressure settings to be increased, consuming more energy. Every 2 psi in extra discharge pressure increases the compressor power consumption by 1%.
The maintenance crew at the plant were surprised to learn of the existence of the filter and quickly obtained a replacement unit. They had been wondering why they were getting complaints of low plant pressure when they knew the compressor discharge pressure had been boosted higher. Once changed, the undesirable pressure loss disappeared and the compressor discharge pressure was lowered to its previous value.
Some air dryer manufacturers have realized that it is easier to filter and remove entrained impurities from cold compressed air because the air is denser at the cold temperatures within a refrigerated air dryer. Thus, “cold coalescing” filters are designed into some dryer enclosures to provide more efficient contamination removal. These filters are sometimes difficult to see, and if maintenance crews are unaware of this, the unmaintained filters can become clogged, causing a high pressure differential.
Filed Under: Components Oil Coolers, Compressed Air Technologies, Pneumatic Tips, Technologies