All trends in mobile machinery development point toward creating more compact, fuel-efficient machines that reduce emissions.
It seems like every day, news is released from key fluid power manufacturers, mobile OEMs themselves, and others about a transformation in off-highway machinery. These innovations are driving a wave of change that promises efficiency, sustainability, and enhanced performance. Key trends steering this evolution include improved hydraulic control, battery electrification, hydrogen power, and autonomy, among other emerging technologies.
Fluid power working towards efficiency
Hydraulics technologies will continue to have a long life on mobile machines, as they have the advantage of power density and cost on their side. But with inherent inefficiencies, it is crucial to improve hydraulic systems. Electronic and digital control is the king here, as manufacturers integrate electric control to reduce losses and integrate systems to make machines more compact and lighter weight.
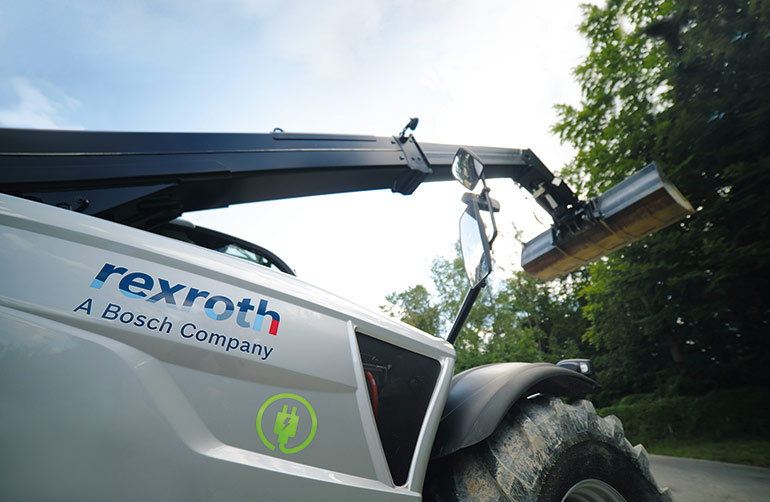
For instance, Bosch Rexroth has been touting its eOC system, which electronically controls hydraulic pumps in open circuits. This solution combines the electrohydraulic eOC pump with a swivel angle sensor and pressure sensors.
Controlled via a CAN interface, the eOC software makes it possible to set various control parameters flexibly during operation. Control modes can be individually changed and combined, and the pump dynamics can be set variably. Pressure, torque, flow, and swivel angle are controlled independently in an electronically closed control circuit.
According to Mauro Silva, sales manager of Mobile Electronics at Bosch Rexroth, a standard pump requires a manual adjustment to the circuit, which means that one function stays with the machine.
“The electronic open center pump control removes all the complexity in the pump that the cylinder requires and does it all electronically,” Silva said. “In the standard load-sense system, you can use pressure control, flow control, or torque control — but you can only have one because it’s a direct linkage to the pump controller. Now, with electronic (control), you can have all three at different times. This is where you can explore the benefits of controllers in the same system without changing the hardware. This enables you to change the operational mode of the pump dynamically.”
The pump’s rotor group has the same efficiency as always, Silva said. “It’s not more efficient, but by enabling you to change this operational mode dynamically, you can reach better performance. This could be translated to more quality, or you can do the same work in less time,” Silva said. “This is where the main fuel consumption reduction comes from, by improving the operation ability of the machine.”
Although they’ve had inquiries for fully electrified whole machines, Silva noted that the costs of the electromechanical actuators push the overall machine cost too high, so this hybrid idea of battery-powered machines with electronically controlled hydraulics still offers the better payback.
Digital control, combined with powerful electronics, allows Danfoss to create more efficient machines. Domenico Traverso, president of the Editron and Incubation Division at Danfoss, said its Dextreme digital hydraulic pump can reduce fuel consumption and emissions by up to 50%, which is enormous for an excavator.
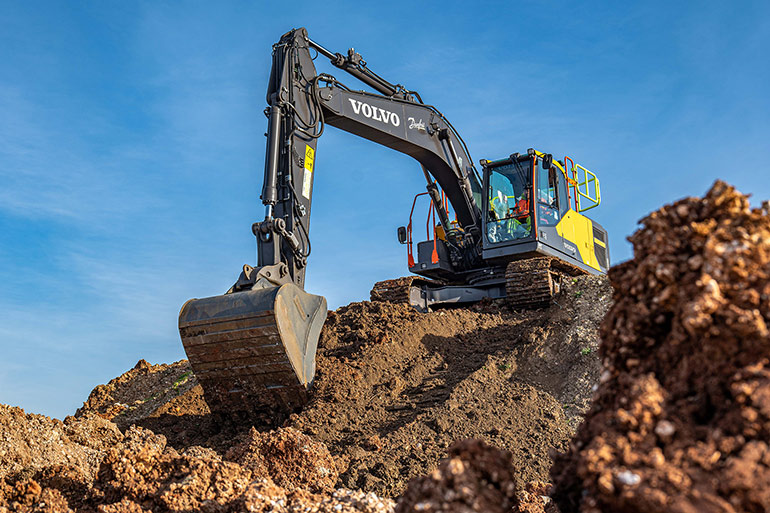
At the core of each Dextreme system is the Danfoss Digital Displacement pump, a digitally controlled hydraulic pump for off-highway machinery. Its dedicated digital controller activates each piston individually, providing fast and accurate response to system demand. The pump provides full and partial load efficiency by using only the pistons needed to meet the load.
Software controls and optimizes each component of an electric or hybrid drivetrain, leading to more intelligent power distribution management. It helps to deliver maximum efficiencies and reduced size and weight. The system is suitable for hybrid and full electric applications within the power range of 30 to 1000 kW.
“If you match that with Editron, you can reduce the battery and make the excavator longer lasting. You would capture all the value of having the digital control of hydraulics on an excavator,” Traverso said. “I can tell you that the business is growing tremendously. We are more than doubling every year.”
At Agritechnica, Editron launched the ED3 onboard charger for off-highway use. Initially designed for on-highway applications, it offers fast, easy access to 43 kW of charging power — currently the highest available. This will allow heavy-duty electric vehicles to be charged overnight using readily available ac power outlets, facilitating quick deployment and minimizing charging infrastructure costs.
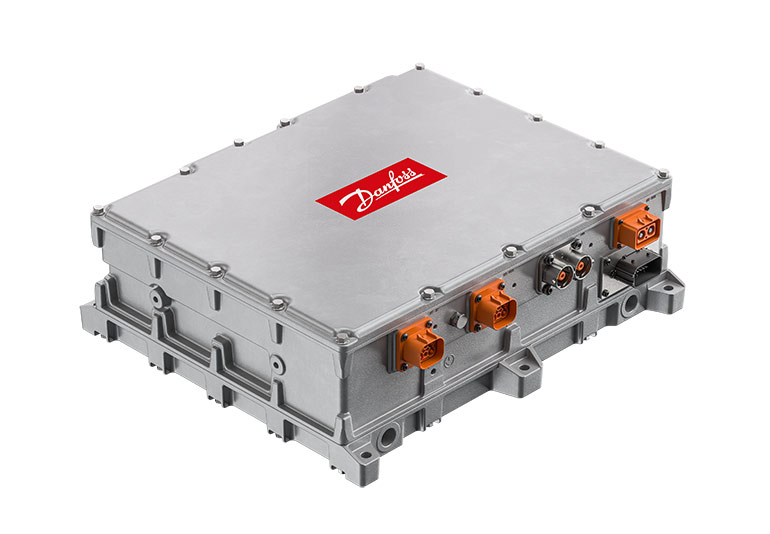
“Rapid ac charging is necessary to eliminate range anxiety for commercial vehicles undertaking deliveries on variable routes and for machines at construction sites without access to dc charging,” said Kimmo Rauma, vice president of Editron at Danfoss.
At IFPE this year, Parker touted its next-generation Global Vehicle Inverter (GVI) with built-in functional safety. The GVI uses the same hardware with two software configurations to provide traction control or hydraulic work functions. It can control an EHP Series Configured ePump, which consists of a Global Vehicle Motor (GVM) directly coupled to a hydraulic pump. The ePump combinations include GVM electric motors with piston, vane, bent axis, and gear pumps.
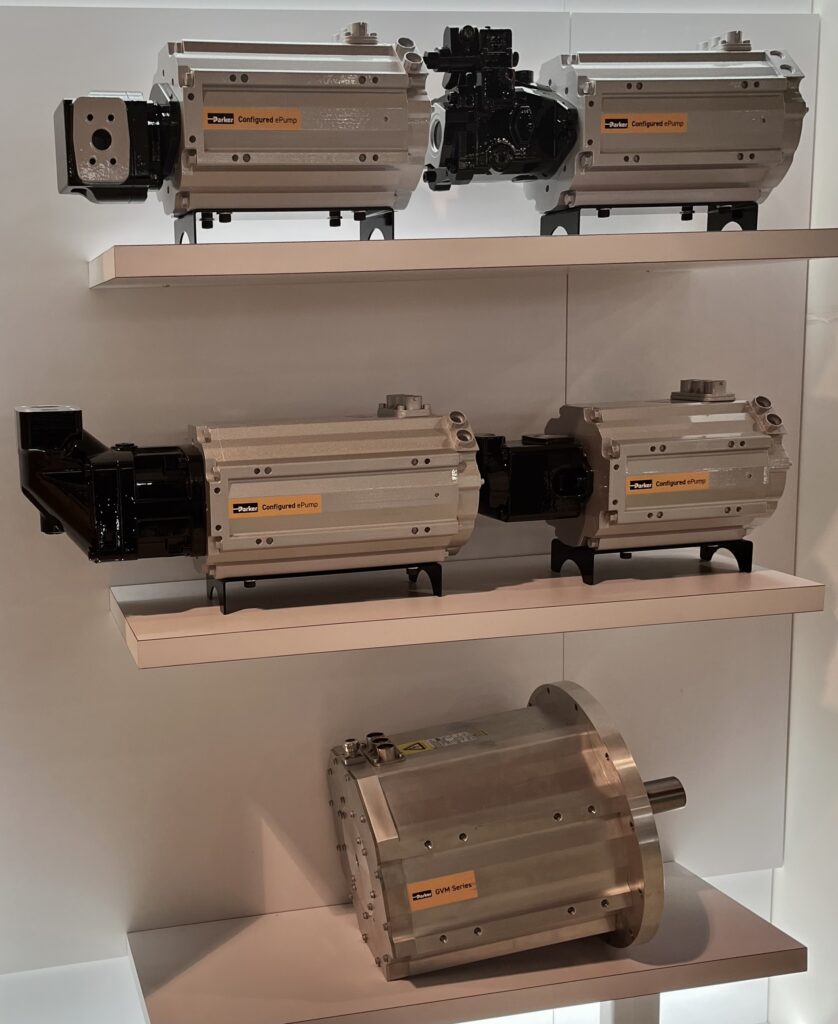
“The GVM is a permanent magnet ac motor with a power-dense design and an integral cooling tube built into the core diameter of the motor. In many cases, you have to put a bulky jacket around the motor. But since we have the cooling tubes inside the motor stator, we can get a lot of power out of a very small piece of equipment,” said Christopher Griffin, business development manager for electrification at Parker.
The booth also had an example ePTO to show how a GVI inverter and ePump could be configured for a truck chassis. The assembly had a two-stage pump and a coolant system with components designed specifically for electric vehicles.
“Now, hydraulics aren’t going away,” said Griffin. “They’re too good at what they do, and we’re not suggesting they should go away. But we can do things to make them more efficient. For instance, the simplest way is to drive all the hydraulics off one motor or start to decentralize the hydraulic functions so that multiple motors only produce power when needed rather than idling.”
Driverless vehicles on the horizon
Integrated autonomous features, driven by artificial intelligence and machine learning algorithms, are enhancing machine and worker safety, efficiency, and productivity. Automation reduces human intervention and allows for precise and efficient execution of tasks, leading to optimized workflows and reduced operational risks.
One such manufacturer highlighting this technology at IFPE this past March was Moog Construction. Moog focuses on its electromechanical technologies but can also create electrohydraulic conversions to ensure the right fit for the right application.
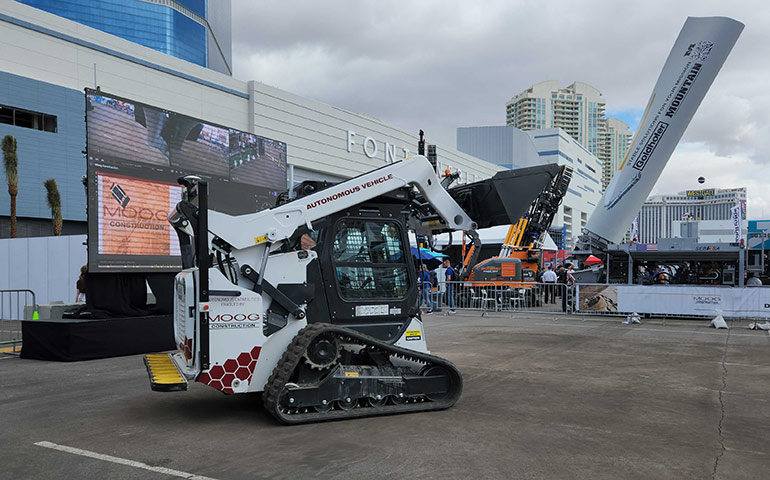
Their demos highlighted heavy-duty, high-precision actuators, motors, drives, thermal and battery management solutions, and electronic control modules. Those technologies showcase precision motion control and automation for dangerous applications, particularly where human and machine interactions are common.
On display was a diesel retrofit kit, but the autonomous platform is easily integrated as an option for electric machines. The technology is being used in massive work trucks in mining, solar fields, and mining demolition to reduce damage risks to machines and work products. Most importantly, it keeps personnel safe.
“The tagline we love to use is anything that’s dull, dirty, or dangerous,” said Nicole Wodka-Cook, now GM of Space Actuation and Avionics with Moog Inc. “Those are ripe for disruption in the autonomous space or semi-autonomous space. It’s where you want to take the human out of it because that work is not satisfying, it’s hard to find labor, or it’s dangerous.”
In other news, Teleo, a company building autonomous technology for heavy construction equipment, is providing its systems to Tomahawk Construction to deploy on an active job site. The Teleo Supervised Autonomy system lets contractors operate heavy equipment without an operator in the cab, so a single person can control multiple pieces of equipment from a remote desk. Tomahawk Construction’s articulated dump trucks will use autonomous functions to move material to build a residential community.
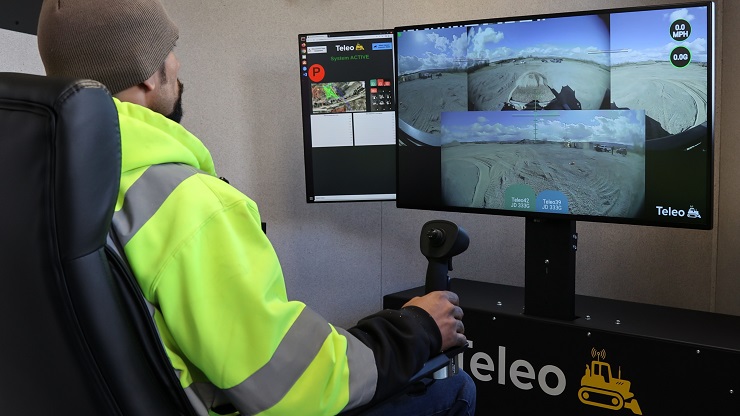
“Teleo’s technology has the potential to completely transform our operations,” said Scott Lyons, managing member of Tomahawk Construction. “With Teleo, two of our dump trucks that have been idle will be put back into service to haul dirt across the site autonomously, allowing our remote operators to do more. This will help us to run a more efficient operation.”
Alternative power through batteries and hydrogen
One of the most profound shifts in mobile machines is the rapid adoption of battery electrification. Lithium-ion batteries are currently the main staple for battery-powered mobile machines (turn to page 11 for a look at sodium ion options). While many battery companies have gone bankrupt this year, it’s not stopping mobile machinery makers from getting in the game.
Just last month, Komatsu America Corp. acquired American Battery Solutions (ABS) in Michigan. ABS manufactures heavy-duty and industrial battery packs, using lithium-ion batteries for commercial vehicles, transit buses, and on- and off-road vehicles.
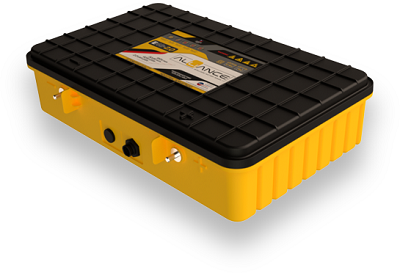
Komatsu plans to develop and produce its own battery-operated construction and mining equipment, starting with power mining equipment in North and South America, where demand for electrification has been increasing. In the future, Komatsu aims to expand with construction equipment and establish a global supply system.
Although it has many detractors, hydrogen as an alternative power transmission source is still being actively researched for commercial use. Last year, we wrote about Liebherr’s hydrogen-fueled internal combustion engines, and now comes news that Caterpillar launched a three-year program to demonstrate an advanced hydrogen-hybrid power solution built on its new Cat C13D engine platform.
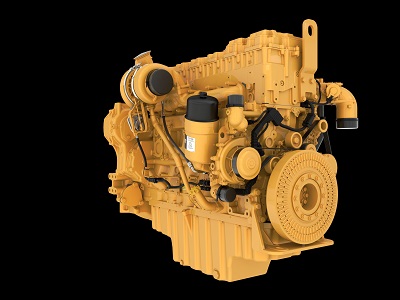
Starting in the first quarter of 2024, Caterpillar will develop a transient-capable system for off-highway applications. The project will demonstrate how state-of-the-art control systems and electric-hybrid components can help hydrogen-fueled engines meet or exceed the power density and transient performance of traditional diesel engines.
The Cat C13D engine is targeted to power a wide range of hydraulics-intensive off-highway equipment. Unveiled at CONEXPO-CON/AGG 2023 in March, diesel-powered versions of the Cat C13D engine offer eight power ratings from 456 to 690 hp (340 to 515 kW) with up to 3,200 Nm of peak torque. It provides up to a 20% increase in power and up to 25% more low-speed torque than the previous generation of Cat diesel engines in its power class.
The inline, six-cylinder Cat C13D enables the use of renewable liquid fuels such as 100% HVO, B100 Distilled Biodiesel, and up to B100 Standard Biodiesel. In addition to hydrogen, its core architecture is designed for the future development of spark-ignited natural gas capabilities. The company expects to offer OEM pilots in 2025 and scheduled production in 2026.
Filed Under: Mobile Hydraulic Tips, Trending