This year, four companies have been recognized in the new combined Fluid Power category of the LEAP Awards (Leadership in Engineering Awards). Since the awards inception, fluid power was broken out into Hydraulics and Pneumatics but have been brought together under one umbrella.
The LEAP awards acknowledges innovation and engineering achievements from around the globe. Our expert independent judging panel received numerous submissions this year and selected 44 gold, silver, and bronze winners and honorable mentions across 14 categories.
This year, Domin took the Gold Award for its High-Performance Hydraulic Valves, with patented rotary valve technology, which have been developed using cutting-edge technologies including additive manufacturing, brushless DC motors, and onboard electronics.
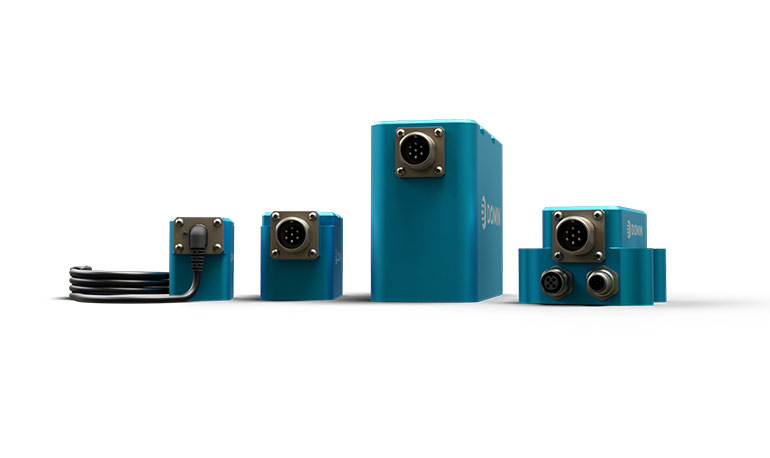
Domin hydraulic valve range
These direct-drive servo valves are as small or smaller than two-stage valves but with benefits of cutting-edge onboard electronics and energy efficiencies. The core elements for Domin’s innovation are:
- Architectural engineering design to create small perfectly manufactured hydraulic valves, using the multi-disciplinary capabilities of our design engineers, making use of CAD integrated analysis tools to quickly iterate the product design and find the best compromise to suit both structural and flow requirements.
- Novel direct drive rotary valve solution, using a rotary motor and rotary spool that creates advanced high-speed hydraulic control.
- Using additive manufacturing to create compact structures that have very low-pressure loss, making the fluid’s journey as easy as possible. In addition, additive manufacturing allows us to print small structures that have inbuilt bi-directional flexibility.
Domin has multiple patents in this area to date, covering valve technology and system integration architectures.
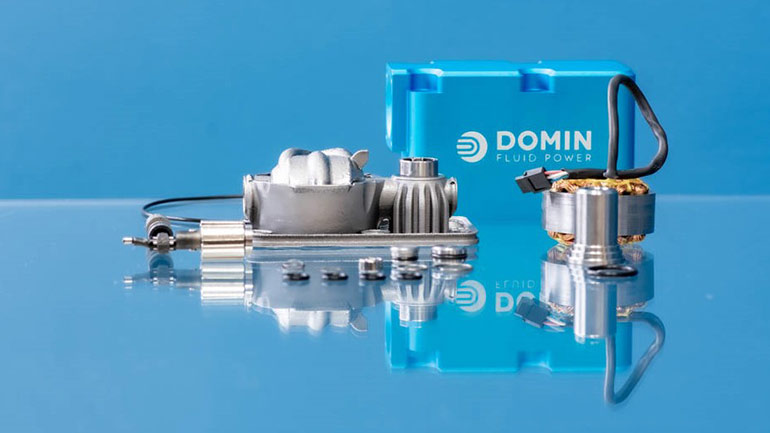
Deconstructed Domin valve
Domin’s high performance hydraulic servo valves deliver increased reliability, performance and profitability.
- More efficiency: Up to 80% less energy loss using direct drive valves, saving $400 per valve per year.
- More power: A more powerful motor paired with an advanced PID controller enables the valve to push through contaminants, and maintain performance beyond the lifespan of competitor valves.
- More precision: Advanced electronics give precise and accurate closed-loop control and modern spool sensing technology.
- More productivity: Fast steps responses of 3ms compared with competitors of over 8 msec, high flow rates, and high frequency response.
- More control: Low hysteresis that give high accurate movement in both directions, low threshold, and low null shift.
- More reliability: Lower servicing costs, as there are no high-pressure seals, no filters, fewer components, simpler assembly, and environmental sealing. With no first stage, all small blockage prone features are removed.
For example, the S4 Pro is a lightweight, high-performance directional flow control valve with onboard electronics that covers a range of rated flows from 0.7 to 18 lpm up to a max pressure of 350 bar per spool land. Based on a port circle of 12.2 mm and with a weight of less than 300g, the S4 Pro is suited to applications requiring superior performance, dynamics, and reliability.
Danfoss notched silver for its Danfoss Thorx CLM 8 S cam lobe motor, which is designed for use in skid steer loaders. A recent motor, the CLM 12 T is suited to compact track loaders. The design has received multiple patents, covering the arrangement of the parts (the rotary group) that enable the shorter length, integral disc brake, and efficiency improvements.

Thorx cam lobe motor from Danfoss
Skid steer loader owners and operators increasingly look for machines that offer higher productivity. To pick up heavier loads, complete tasks faster, and increase travel speed, skid steers are being designed to deliver higher power and more force. Smooth, predictable operation is no longer a desire; it’s a demand.
High-pressure hydraulic pumps are delivering the power skid steers need, but traditional orbital motors do not offer the best efficiency; they also can’t match the performance of higher pressure pumps. Cam lobe motors offer higher pressure ratings and greater efficiency, delivering 30% more force. However, two-speed shifting, package size, and efficiency throughout the speed range are some of the shortcomings.
Two-speed motors support the industry drive for greater productivity, delivering higher torque when working and higher speed when roading. But a problem arises when shifting between these two. A sudden change in the wheel speed or torque can be quite shocking for the operator as well as the vehicle, leading to discomfort, instability, and the possibility of a lost load. The effect is worse when the machine is cold. Shocks can be erratic or delayed, undermining driver confidence. With motors positioned back-to-back in skid steer loaders, length is important. Typical cam lobe motors have a large envelope, which can make assembly and service a challenge in compact machines.
The Thorx cam lobe motor solves many of of the challenge facing skid steer loader designs. Compared to other cam lobe motors on the market, the Thorx motor reduces shock at speed changeover by 70% and eliminates inconsistencies due to temperature, resulting in smoother, more predictable machine handling. The significant reduction in shock is made possible through innovative system software with complex signaling and feedback loops.
Thorx motors feature a larger diameter rotary group that enables the parking brake to be integrated in the center, rather than bolted to the rear. This configuration makes the motors 33% shorter in length than competitive motors, with only a negligible 1-cm increase in width. Reducing the motor’s space claim simplifies installation and frees OEMs to increase the size of the chains driving the wheels, which can increase the life of the machine.
The increased space created by the larger rotary group enables a return to proven multidisc brake technology. Other cam lobe motors use dog clutch brakes, which generate harsh emergency stops and wear out extremely quickly — sometimes in as few as one or two emergency stops. The more conventional multidisc brake offers strong parking torque as well as smooth emergency stopping. The Thorx motor’s brake is designed to withstand 100 dynamic emergency stops.
The final advantage of the motor’s larger rotary group is reduced friction and flow losses, which increases the starting efficiency as well as high-speed efficiency by 5%.
At the Bronze is Gefran with its TWIIST Contactless Linear Position Transducer. Gefran also won the Gold for the TWIIST in the LEAP Sensors category. TWIIST is a contactless linear position transducer in the Hall effect category. In addition to processing position data, its unique helical magnetoelectronic design measures other process variables — temperature, velocity, acceleration, and tilt angle — to improve machine designs and performance and increase operator safety. This patented technology results from a decade-long partnership between Gefran’s internal R&D department and the University of Brescia’s engineering department in Brescia, Italy.
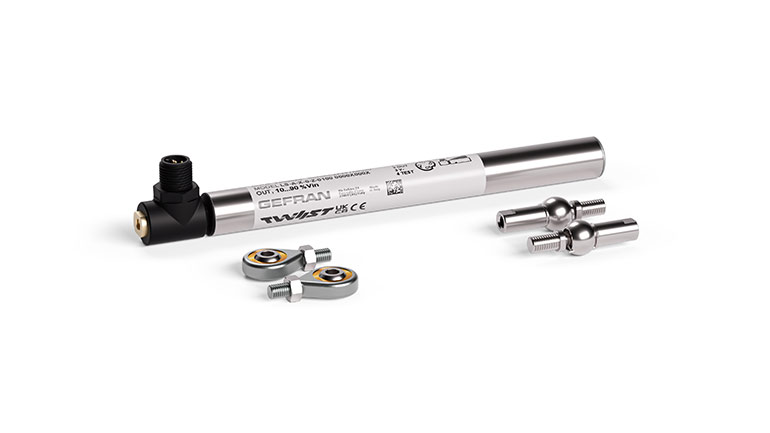
Gefran’s TWIIST multivariable position transducer
TWIIST’s compact, air-tight design has a steel barrel with a diameter of 5/8 in. (16 mm), and it comes with a choice of two types of connection points, ball joints for swivel connections and rod ends with eyes for pivot connections. Available in full-scale (FS) strokes from 50 to 900 mm, it has typical linearity of 0.15% FS and typical repeatability of 0.05% FS. It can operate in a temperature range from -40° to 185°F (-40° to 85°C). Currently, there are three models in the TWIIST product line. There is the LM-L (IO-Link) and LM-C (CANopen) that can transmit measurements digitally up to 1,000 times per second. The LS-A has a mono-variable analog output (current, voltage, or ratiometric), as well as the redundant ratiometric version to support safety applications.
TWIIST covers application needs that are barely met today by other measuring technologies in the market. Magnetostrictive and LVDT technologies for measuring linear position are very accurate but have limited mechanical flexibility and are quite expensive. Alternatively, potentiometric technology is cheap and mechanically flexible, but it is underdeveloped regarding communication protocols. The technology is less resistant to water, shocks, and vibrations, thus making it less reliable.’
The TWIIST is self-aligning, has IP67 protection, and is affordably priced by comparison. This means users get more features and power for less money. TWIIST measures position, while simultaneously measuring linear acceleration, angular velocity, and sensor temperature. It can also implement virtual speed and inclination sensing based on a summary of position and acceleration measurements.
All these features provide a more effective characterization of the device’s operating state, as well as data on the state of the process itself which the TWIIST’s CPU can rapidly analyze and correlate. This makes TWIIST a real cutting-edge computing device and a rarity in the marketplace. For the end user, TWIIST offers a simplified proportional system that is easier to use and maintain. Plus, in keeping up with the changing pace of technology, if new firmware features and enhancements enter the market, Gefran will provide version updates that can be made locally.
Finally, an Honorable Mention goes to Moog Inc. for its Electro-hydrostatic Pump System (EPS), which consists of an Electro-hydrostatic Pump Unit (EPU) and a standardized manifold with hydraulic accumulator. It is offered as a complete system without actuator and can be easily integrated into existing or new machines/retrofits. The Moog EPS is a compact and modular off-the-shelf product available in various sizes and performance levels. The standard components offer a high degree of freedom for end-users and operators through easy integration and scaling, thereby reducing the development and assembly times for a faster time-to-market.
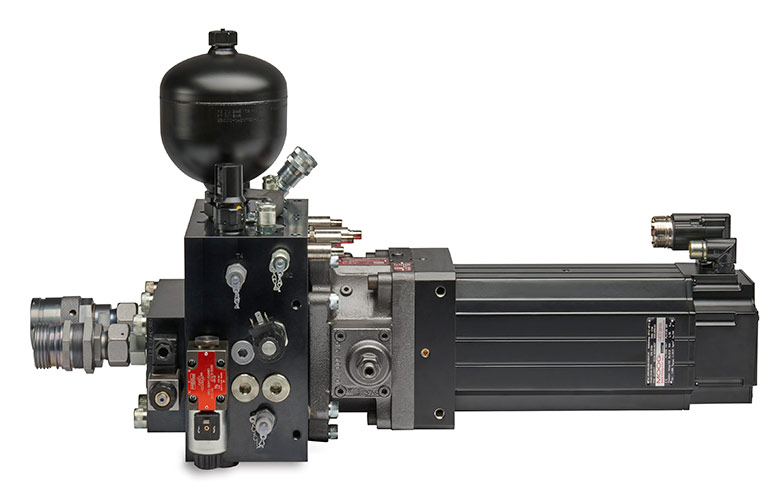
Moog’s Electro-hydrostatic Pump System (EPS)
The Electro-hydrostatic Pump System can be operated in a half-open or closed circuit and provides a modern replacement for traditional hydraulic motion control designs with large HPU’s and piping/hosing. The energy-efficient system is easy to maintain, highly adaptable and allows the use of existing customer components such as cylinders.
The EPS enables, for example, variable displacement with significant speed and force phases and offers high performance and robustness for various applications such as die cushion systems, test and simulation platforms, metal forming and presses, hydraulic pressure intensifiers, marine, and offshore applications, as well as mobile machines with hybrid or fully electric drive concepts.
A streamlined design of the system peripherals can reduce the size and power of the electronic components and thus the connected load. In combination with intelligent energy management, this leads to significant savings in overall energy consumption in the medium to long term. Moog offers a wide range of suitable power electronics and software solutions to
exploit this potential.
Filed Under: Components Oil Coolers, News, Pumps & Motors, Sensors, Sensors & Gauges, Valves & Manifolds